Rolling Chassis von Benteler und Bosch: Die fahrende Werbe-Plattform
Mit dem gemeinsam entwickelten Rolling Chassis wollen die beiden Zulieferer Bosch und Benteler nicht selbst in die Autoproduktion einsteigen, wohl aber ihre Kompetenzen erweitern. Mögliche Kunden sollen aus verschiedensten Modulen wählen können – bis hin zu einer nahezu kompletten Plattform. Eine erste Mitfahrt zeigt, welches Potenzial die Entwicklung bietet.
* * *
Es ist extrem ungewöhnlich, wozu Bosch und Benteler in die Werkstatt 1 des Prüfzentrums Boxberg geladen haben. Frühe Technik-Prototypen und Entwicklungsträger werden für gewöhnlich unter Verschluss gehalten. Vielleicht gibt es einige PR-Fotos aus wohl gewählten Winkeln, um nicht zu viel zu verraten. Auf Messen stehen dann aufwändig präparierte Schnittmodelle – wieder mit dem Ziel, Einblicke zu geben ohne dabei die eigenen Entwicklungen preis zu geben.
In der Werkstatt 1 steht allerdings das Rolling Chassis. Eine von Bosch und Benteler entwickelte Elektro-Plattform, die Batterie, E-Motoren und alle für das Fahren wichtigen Komponenten vereint. Für die Erprobungsfahrten wurden ein Lenkrad, zwei Schalensitze mit Vier-Punkt-Gurten sowie ein Überrollkäfig installiert – fertig ist das Auto. Mit all den Laptops, offen verlegten Kabeln und der Abwesenheit sämtlicher Komfort-Features wirkt das Rolling Chassis auf den ersten Blick eher wie ein Bastel-Projekt mehrerer Technik-Studenten als die Vorstufe zu einem luxuriösen Premium-SUV.
Doch genau das ist das Rolling Chassis. „Wir haben das Fahrzeug nach einem Kundenprojekt ausgelegt“, sagt Dieter Schwarzmann, der den Bosch-Teil des Projekts leitet. „Auch wenn es nicht so aussieht, das hier ist ein großes SUV mit 2,45 Tonnen Leergewicht und drei Metern Radstand.“ Um das spätere Gewicht des fertigen Autos mit der Karosserie und dem Innenraum zu erreichen, wurde das Rolling Chassis mit Stahlplatten beschwert. Und die ganzen Kabel? „Alles nur unsere Messtechnik für die Entwicklung. Würden wir das ausbauen, wäre es eine sehr aufgeräumte und reduzierte Plattform.“
Das Kundenprojekt ist das zweite Serienmodell von Automobili Pininfarina. Die Marke will nach dem Supersportwagen Battista weitere elektrische Modelle folgen lassen und arbeitet dabei mit Benteler und Bosch zusammen. Zudem hat der chinesische Immobilienkonzern Evergrande für seine Elektroauto-Pläne im vergangenen September eine Lizenz des „Benteler Electric Drive System 2.0“ – also quasi einer verwandten Vorstufe des Rolling Chassis – von dem Paderborner Zulieferer für seine kommenden Hengchi-Modelle erworben.
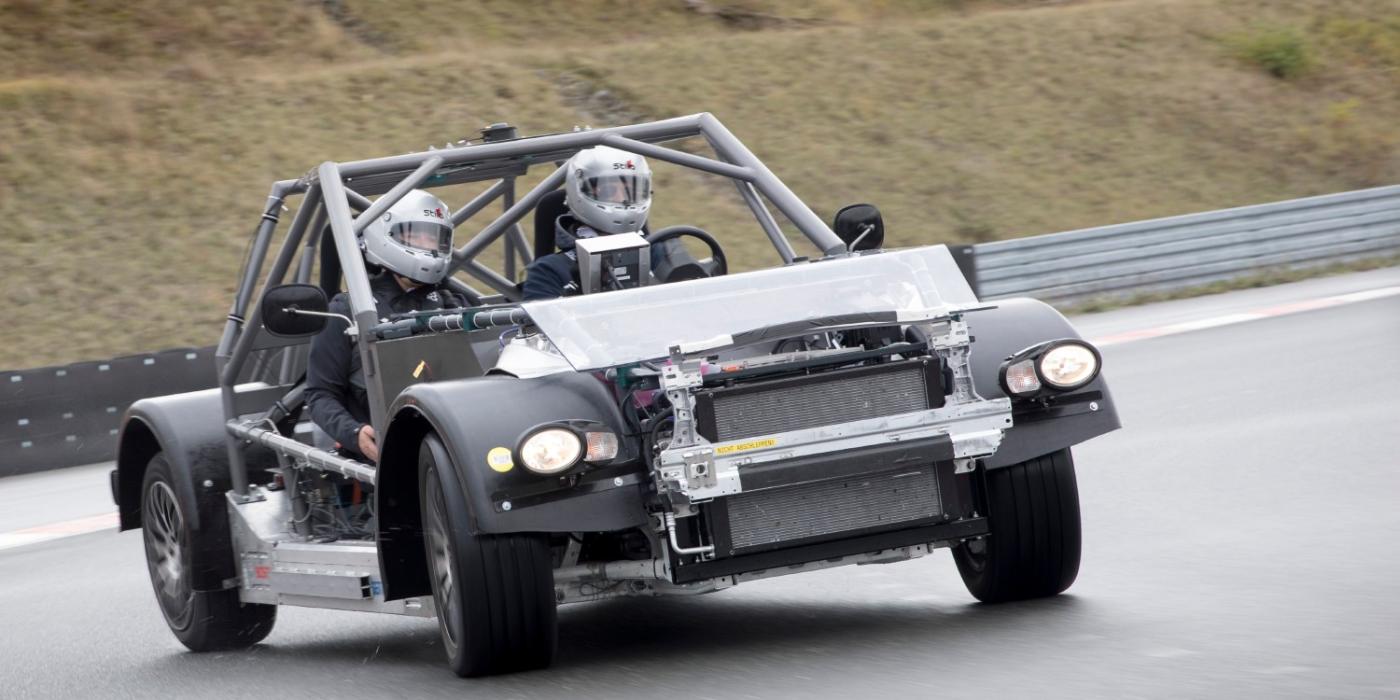
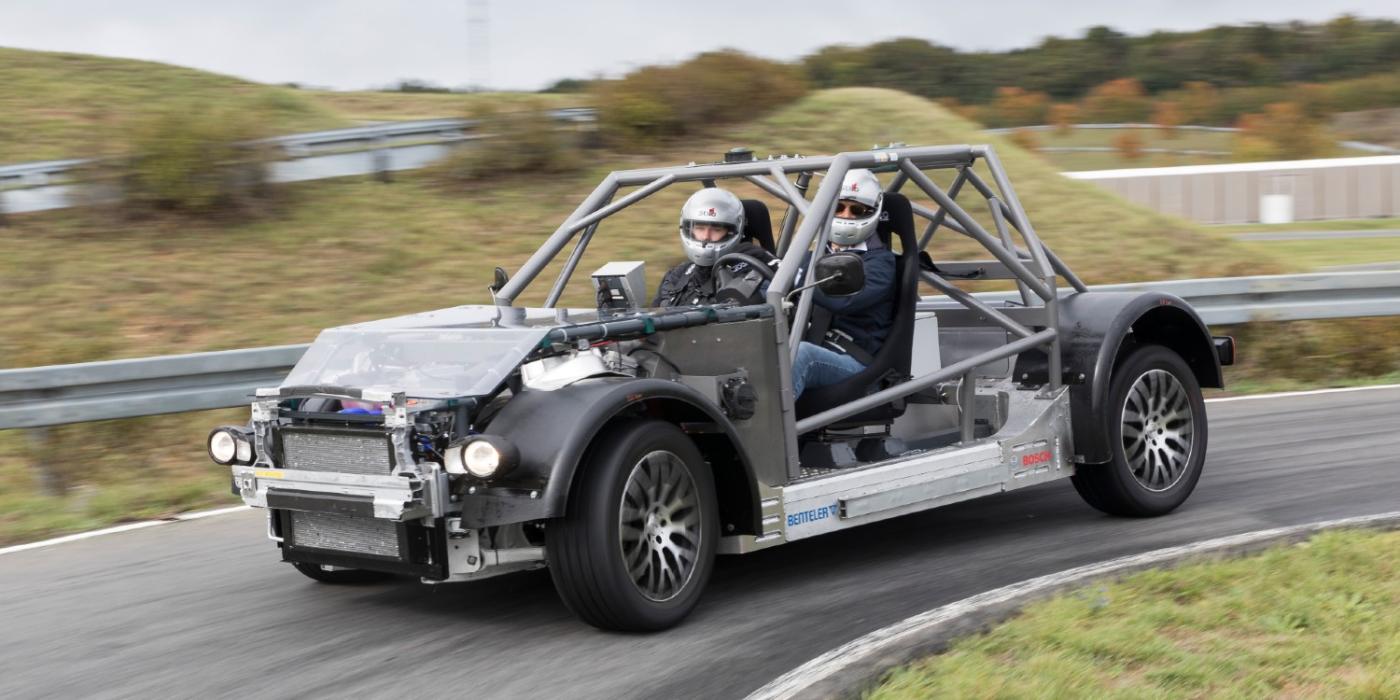
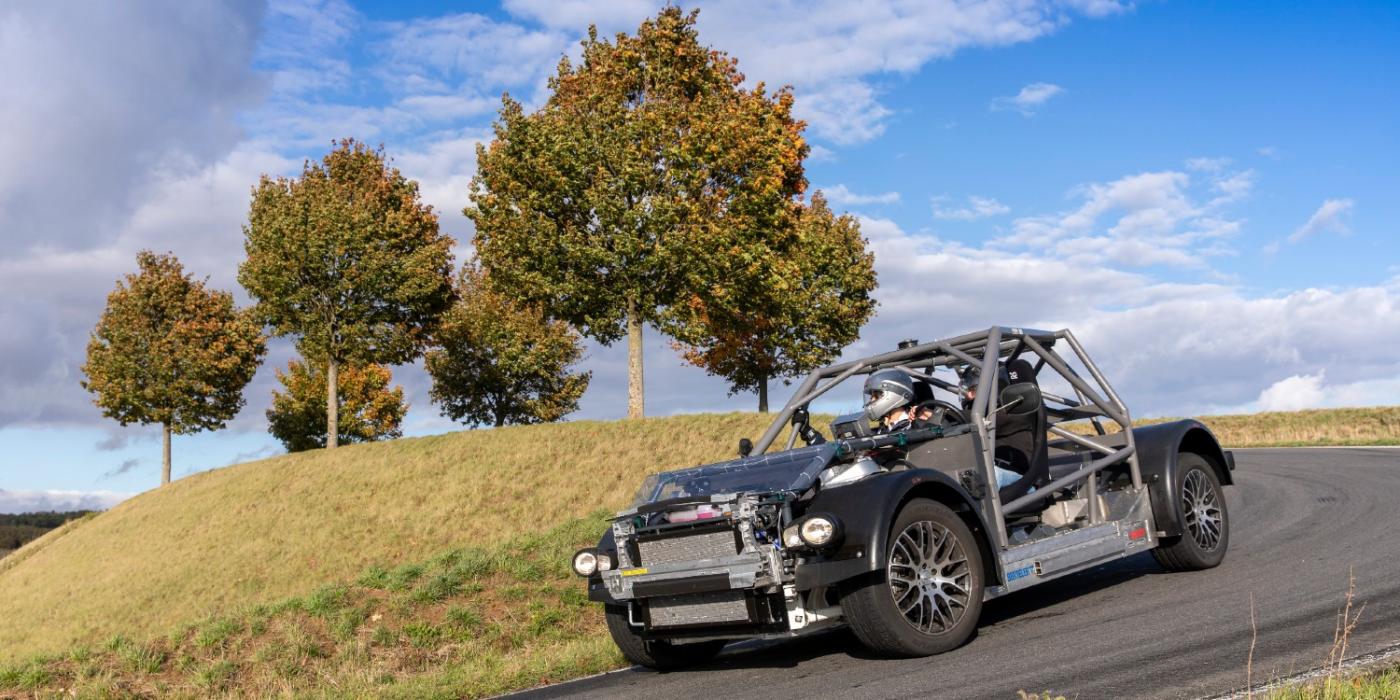
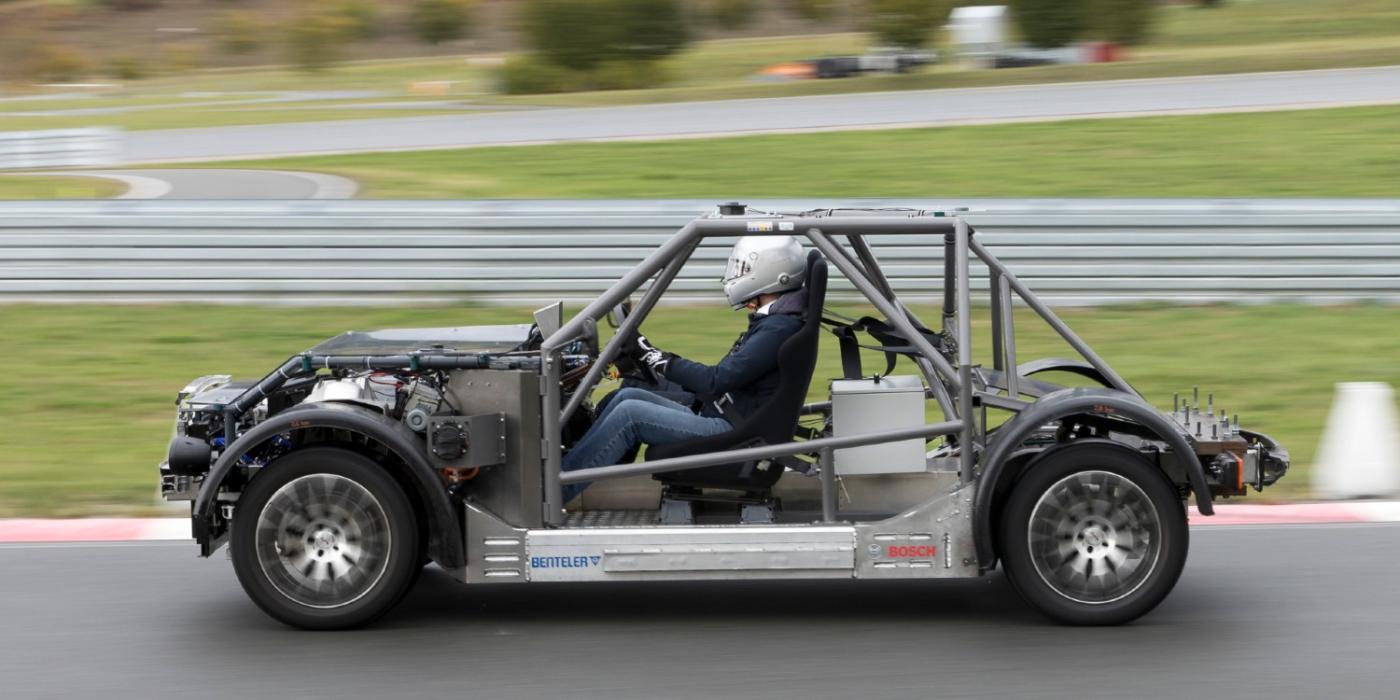
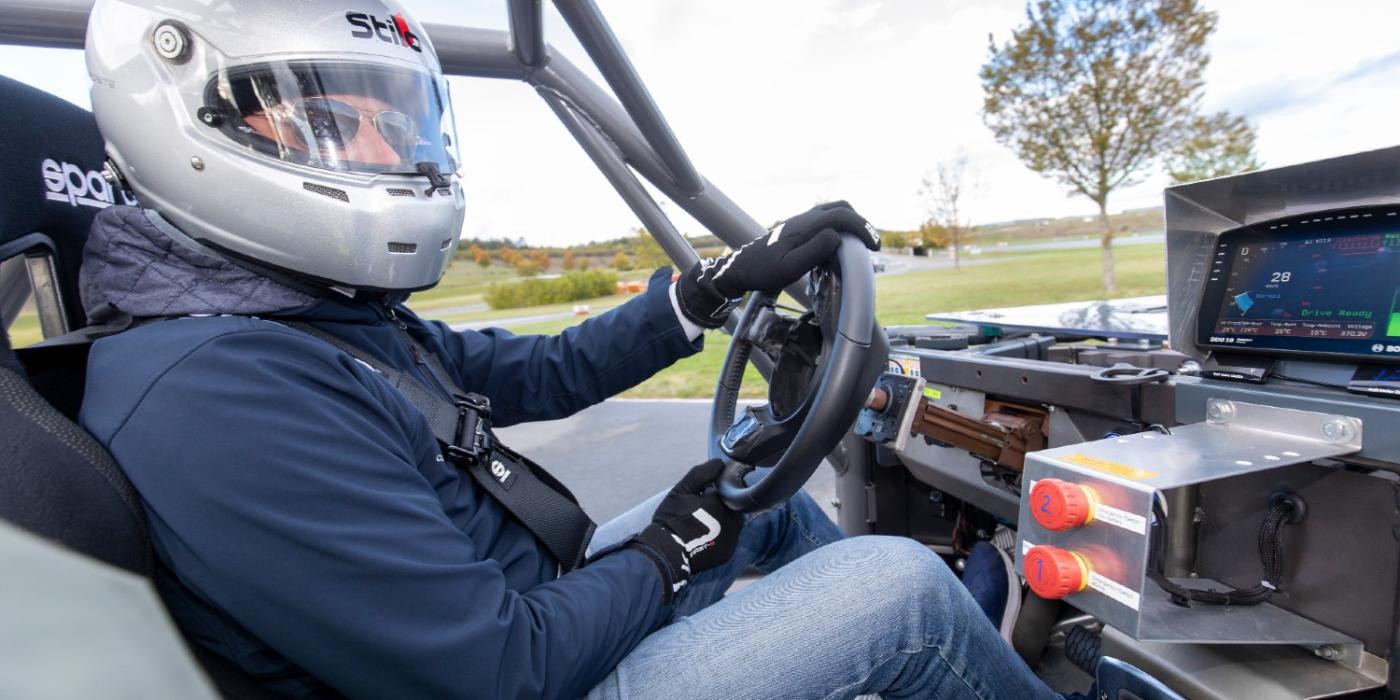
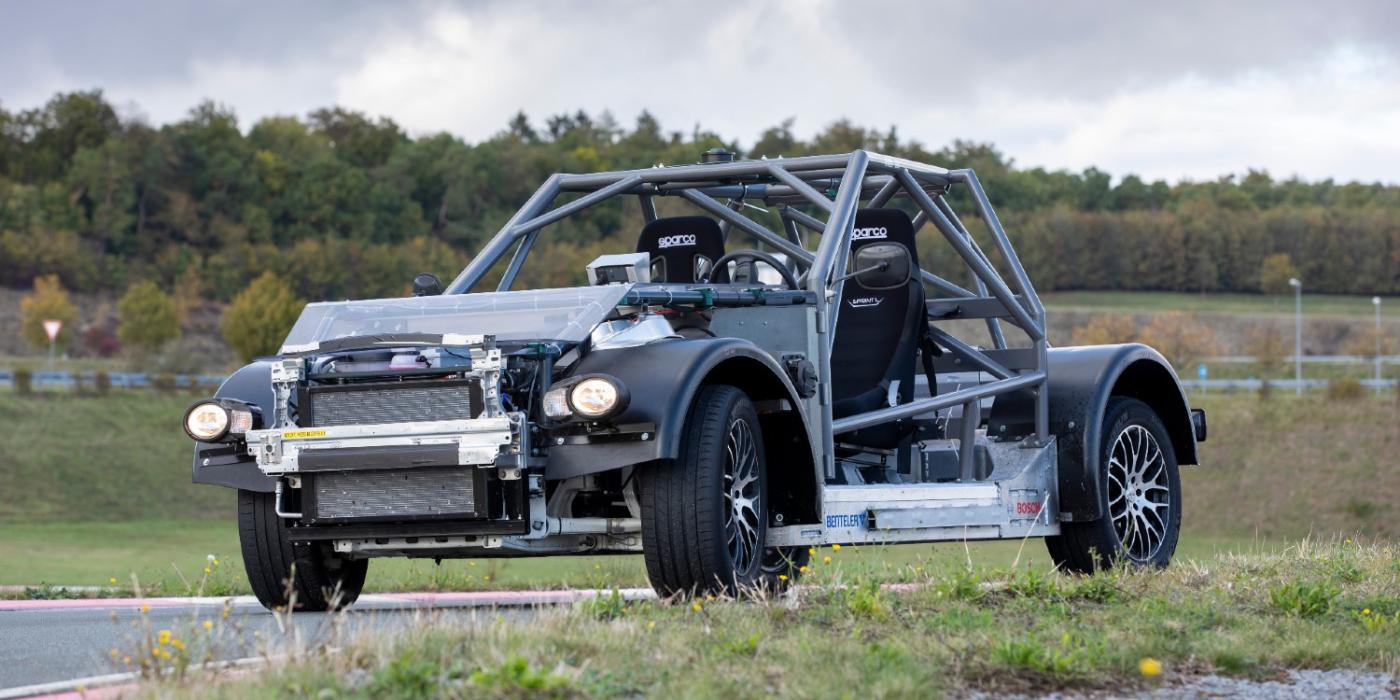
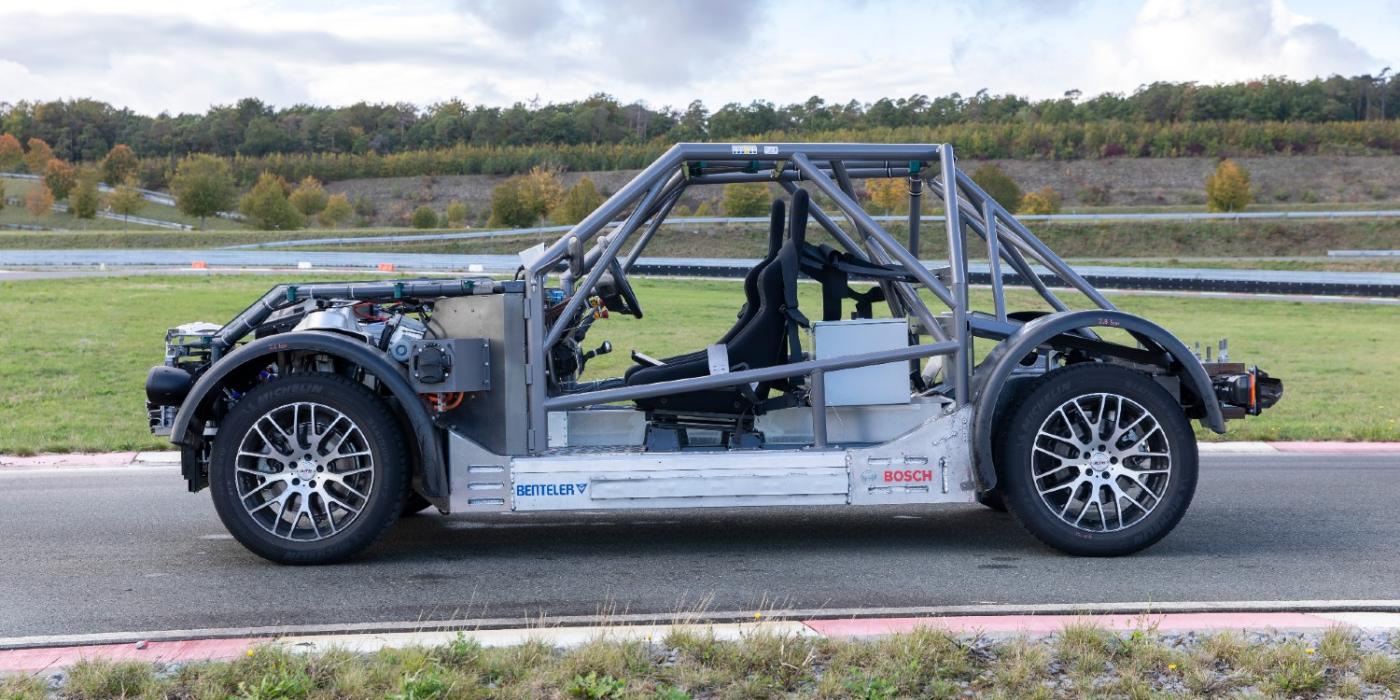
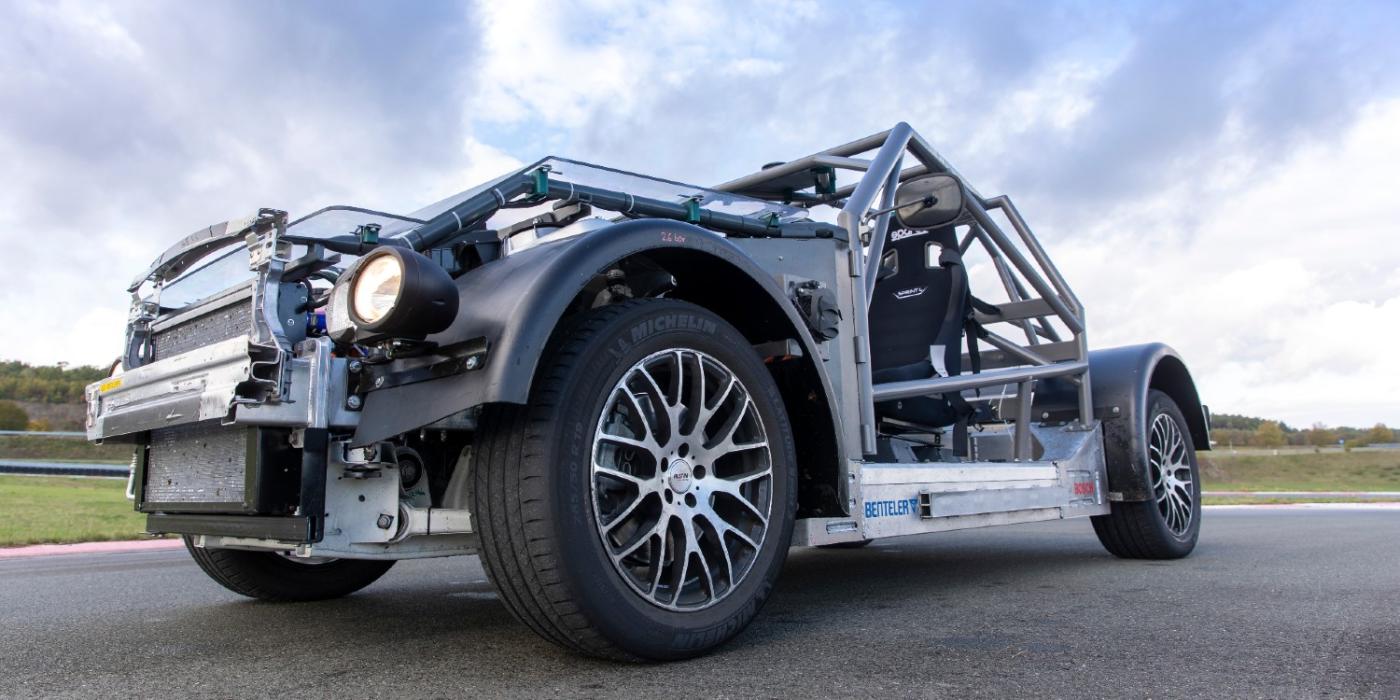
Laut Rodscha Drabon, dem verantwortlichen Projektleiter der Benteler-Seite, könnten auf der Technik des Rolling Chassis verschiedene Fahrzeuge des D- und E-Segments, also der Mittel- und Oberklasse, aufbauen. Besonders erwähnt er aber den Radstand von genau drei Metern, wie ihn etwa ein Tesla Model Y biete. „Deutsche OEM sind aufgrund ihrer bestehenden Produktionsanlagen oft auf einen maximalen Radstand beschränkt, der je nach Hersteller, Plattform und Werk zwischen 2,82 und 2,98 Metern liegt“, sagt der Ingenieur. Mit den Extra-Zentimetern beim Radstand könne bei gleicher Fahrzeuglänge ein größerer Innenraum erreicht werden.
Und ein größerer Radstand schafft mehr Bauraum für die im Unterboden verbaute Batterie. Bis zu 100 kWh seien möglich, das Rolling Chassis verfügt über eine 84-kWh-Batterie. Die Prototypen-Batterie könne mit bis zu 100 kW geladen werden, so Drabon. Was nahe legt, dass die Zellchemie und Ladeelektronik des Serienfahrzeugs eine andere sein wird. Der Batteriekasten ist eine Benteler-Entwicklung, die darin verbauten Module wurden zusammen mit einem Partner entwickelt.
Der Antrieb des 400-Volt-Systems erfolgt über zwei Elektromotoren mit jeweils 150 kW, einer pro Achse. Möglich sind laut Schwarzmann bis zu 200 kW je Motor, was einer Systemleistung von 400 kW bzw. 544 PS entspräche. Im Rolling Chassis sind es aber 300 kW bzw. 408 PS.
Vorintegrierte Module können kombiniert werden
An dem Einbau der Elektromotoren zeigt sich, wie die Zusammenarbeit der beiden Zulieferer im Detail aussieht: Anders als die großen Verbrenner werden die kleineren Elektromotoren nicht direkt mit dem Chassis verbunden, sondern in einen Hilfsrahmen eingesetzt, der dann wiederum am Chassis befestigt wird. Während sich Bosch um den E-Motor, die Leistungselektronik und an der Vorderachse etwa das Lenksystem (über die Tochter Bosch Automotive Steering) kümmert, hat Benteler den Achshilfsrahmen entworfen – ein Bauteil, an dem Partner Bosch wiederum kein Interesse hat.
Derartige Hilfsrahmen sind bei Elektroautos deutlich komplexer als bei Verbrennern. Da sie nicht nur der Befestigung einiger Bauteile dienen, sondern mit dem E-Motor sämtliche Antriebskräfte (und auch umgekehrt bei der Rekuperation) übertragen, müssen die Achshilfsrahmen anders ausgelegt werden, wie Drabon erklärt. Bei dem Rolling Chassis ist der Rahmen aus Komplexitätsgründen aus Stahl, für Kunden seien aber auch Alu-Rahmen möglich.
„Zusätzlich zu den Antriebskräften haben wir bei den Achshilfsrahmen speziell auf deren NVH-Verhalten, also Noise, Vibration und Harshness geachtet“, sagt der Benteler-Projektleiter. Der Hilfsrahmen an der Vorderachse ist an sechs Punkten mit Gummilagern am Chassis befestigt, hinten sind es vier Punkte. Da die an den Hilfsrahmen verbauten E-Motoren auch mit Gummilagern befestigt sind, werden die Antriebskräfte sogar doppelt entkoppelt.
Selbst im Regen überrascht das 2,45-Tonnen-SUV
Ein Aufwand, der selbst in dem komplett offenen Rolling Chassis während der Mitfahrt mit Bosch-Entwickler Schwarzmann am Steuer zu spüren ist. Die Windgeräusche pfeifen zwar um den notwendigen Helm, ungewünschte Vibrationen beim Beschleunigen und Rekuperieren sind nicht vorhanden. Selbst bei starken Lastwechseln verhält sich der 300-kW-Antrieb aus NVH-Sicht ausgesprochen komfortabel.
Auch das Fahrwerk wirkt für das Fahrzeug – wohlgemerkt ein 2,45-Tonnen-SUV – sehr dynamisch. Auf der regennassen Handlingstrecke in Boxberg ermöglicht das Rolling Chassis – dem hohen Gewicht und relativ abgefahrenen Reifen zum Trotz – erstaunliche Kurvengeschwindigkeiten. Dabei bleibt das Fahrzeug auch sehr gutmütig und neigt nur leicht zum Untersteuern. Erst bei einem provozierten Lastwechsel bricht die Hinterachse aus: An dem Rolling Chassis war während der Testfahrt eine starre Rekuperation von 50 Prozent der Antriebsleistung eingestellt – sobald Schwarzmann vom Gas geht, bremst jeder der Motoren mit 75 kW. Auf der nassen Fahrbahn sind plötzliche 75 kW Bremswirkung an der Hinterachse für die Reifen in der Kurve zu viel. Wie Schwarzmann betont, sei das eine für die Testfahrt gewählte Einstellung, eine dynamische Verteilung der Antriebs- und Rekuperationsleistung sei auch möglich.
Das Fahrwerk besteht aus einer Double-Wishbone-Konstruktion vorne und einer Fünflenker-Aufhängung hinten. Das Rolling Chassis verfügt über Stahlfedern, optional sind laut Drabon auch adaptive Dämpfer, eine Luftfederung und trotz des Bauraums des E-Motors auch eine Hinterachs-Lenkung möglich. Nur auf eines haben Bosch und Benteler verzichtet: eine aktive Wankstabilisierung. „Mit der Batterie sitzt der Schwerpunkt so tief, dass ein klassischer Stabilisator ausreicht“, sagt Drabon.
Zulieferer erschließen sich neue Geschäfte – auch wegen anderer Nachfrage
Doch wozu der ganze Aufwand? Die beiden Zulieferer wollen nach eigenen Angaben das Rolling Chassis selbst als Plattform nicht unbedingt vermarkten. Ihnen geht es um die für das Fahrzeug entwickelten Module. „Batterie-elektrische Fahrzeuge erfordern neue Architekturen, da deren Lastenhefte sich von Verbrennern unterscheiden“, sagt Ulrich Schulmeister, Vice President of Engineering bei Bosch. „Typische, markenspezifische Antriebssysteme sind nicht mehr vorhanden bzw. andere Funktionalitäten übernehmen die Markendifferenzierung. Geringere Stückzahlen erfordern hohe Modularität, um wirtschaftliche Entwicklungs- und Herstellkosten abzubilden.“
Zudem würden die OEM verstärkt Systemlösungen anstatt einzelner Komponenten nachfragen. Dafür sollen vorintegrierte Komponenten – etwa das Advanced Driving Module von Bosch, das eAchse, Bremssystem, Lenkung und Steuereinheit kombiniert – von Benteler mechanisch in das Chassis integriert werden. Dabei können die Kunden (wie etwa Pininfarina) mehr oder weniger das Komplettpaket buchen, andere zielgerichtet die für sie relevanten Module und Komponenten heraussuchen. Das Rolling Chassis sei quasi die höchste Ausbaustufe der Modul- und Komponenten-Logik und zeige was maximal an Integration möglich sei.
„Die OEM stufen immer mehr Komponenten als nicht-markendifferenzierend ein“, sagt Bosch-Entwickler Schwarzmann. „Die Autobauer bekommen dann von uns viel Ingenieurs-Arbeit, die ihre Marke nicht tangiert, bereits fertig entwickelt und abgestimmt.“ Ein Beispiel: Jedes Elektroauto verfügt über einen DC-DC-Wandler, der das Hochvolt-System der Antriebsbatterie mit 400 (oder 800) Volt mit dem 12-Volt-System für etwa Scheinwerfer, Infotainment und die Steuergeräte verbindet. Eine andere unverzichtbare Komponente ist der AC-Onboard-Charger zum Laden des Autos mit Wechselstrom. Bei beiden Komponenten gibt es feste Markt-Standards, weshalb sich ein Autobauer hier nicht von der Konkurrenz abheben kann. Bosch hat daher beide Komponenten in ein einbaufertiges Bauteil integriert und bereits im Vorfeld mögliche Probleme bei der Integration wie elektromagnetische Störungen gelöst.
Dieses Bauteil ist ein Beispiel, aber für Zulieferer ein großer Schritt. Als Tier-1-Zulieferer hat der Konzern zwar bereits früher Bauteile anderer Zulieferer integriert, auf dem Level größerer Systeme lag diese Aufgabe aber bei den Autobauern selbst – die Kombination und Abstimmung verschiedener Zuliefererteile ist bei den heute gängigen Fertigungstiefen eine wichtige Kompetenz. „Um unseren Kunden neue Angebote machen zu können, mussten wir selbst die Kompetenz bei der Systemintegration erst einmal aufbauen“, sagt Schwarzmann. „Dafür erhält der OEM Komponenten, die bereits fertig zu einem Teil-System zusammengefügt und perfekt aufeinander abgestimmt sind – womit er vor allem bei nicht-markenrelevanten Teilen in der Entwicklung viel Zeit und Geld sparen kann.“
Neue Lerneffekte durch das Rolling Chassis
Dabei bleibt es dem Autobauer überlassen, was er als markenrelevant einstuft und was nicht. So manch etablierter Hersteller mag sich noch über ein spezielles Fahrverhalten differenzieren und will daher Federung und Aufhängung selbst integrieren – greift aber dennoch gerne zum hinteren Achshilfsrahmen samt E-Motor und bucht womöglich noch die Hinterradlenkung dazu. Ein Startup, das sich aber vor allem über das Design seines Autos, den Innenraum und die Connectivity vom Wettbewerb abheben will, bestellt eher auch das Fahrwerk oder den komplett vorintegrierten Achshilfsrahmen mit Motor, Elektronik und Lenkung dazu – so die Hoffnung der Zulieferer.
Wobei Benteler-Manager Drabon auch betont, dass selbst mit den bereits entwickelten Modulen samt der Software die unterschiedlichsten Fahr-Charakteristika möglich seien. Während es manchmal auf eine Kombination der Module und Komponenten oder eine neue Fein-Abstimmung hinauslaufe, müsse ein Bauteil aber beinahe in jedem Fall angepasst werden: der Achshilfsrahmen. „Was wir hier als vorderen Hilfsrahmen verbaut haben, ist nur ein Beispiel, sagt Rodscha Drabon. „In der Praxis muss der Hilfsrahmen an das jeweilige Fahrzeug des Kunden angepasst werden, etwa wegen der Befestigungspunkte an der Karosserie.“ Aber auch wegen der Crashtest-Anforderungen, bei denen der Hilfsrahmen mit der umgebenden Karosserie des OEM zusammen wirken muss.
Dieter Schwarzmann betont noch einen Vorteil des Projekts „Rolling Chassis“: „Das Rolling Chassis hat uns auch intern bei der Entwicklung der eigenen Komponenten geholfen“, so der Entwickler. „Was uns bei dem Aufbau und Test des Fahrzeugs aufgefallen ist, fällt wahrscheinlich auch unseren Kunden, also den Autobauern, auf. Anstatt erst auf ihr Feedback zu reagieren, können wir ihnen mit dem neuen Wissen direkt die passende Komponente anbieten.“ Einen Lüfter, den Bosch bisher zugekauft hatte, will der Zulieferer jetzt übrigens selbst entwickeln. Das Zukauf-Teil sei für seine Leistung einfach zu laut gewesen.
1 Kommentar