Logistik-Experiment: Batteriewechsel für Kolosse
Wie können E-Lkw auf mittleren Distanzen von bis zu 300 Kilometern genauso flexibel eingesetzt werden wie Diesel-Lkw? Auf diese Frage hat das Projekt „RouteCharge“ eine bemerkenswerte Antwort gefunden: nämlich durch den Einsatz eines intelligenten Batteriewechselsystems. Hier geht es zum Zwischenfazit.
* * *
Unter 15 Minuten dauert der schwergewichtige Batteriewechsel, für den die Projektpartner eine völlig neue Infrastruktur erschaffen haben. In der Hauptrolle: Zwei Batterieblöcke à zwei Tonnen, die einen aufwendig umgerüsteten 18-Tonner in Diensten der Osnabrücker Spedition Meyer & Meyer mit Strom versorgen. Noch bis Jahresende läuft der Feldversuch auf einer 250 Kilometer langen Pendelstrecke zwischen Peine und Berlin. Sowohl an diesen beiden Endpunkten als auch auf halber Strecke haben die Initiatoren des Projekts aus dem Technologieprogramm „IKT für Elektromobilität“ Batteriewechselstationen errichtet.
Warum der ganze Aufwand? Nachladen dauert bei den derzeit verfügbaren Ladesäulen für Nutzfahrzeuge stundenlang, äußert Dr. Clemens Haskamp im Interview. Der Geschäftsführer der MC Management GmbH, die bei dem Projekt die Konsortialführung innehat, nimmt uns mit hinter die Kulissen der Wechselstationen. Er erläutert, nach welchem Prinzip die Batterien abwechselnd Fahrstrom liefern und das Netz stabilisieren und wie viel Erfindergeist vonnöten war, um sich alle benötigten Spezial-Komponenten selbst zu kreieren.
Im Gespräch mit electrive.net-Redakteurin Cora Werwitzke führt Haskamp aus, dass der E-Lkw – übrigens mit Anhänger – nach Projektende bei Meyer & Meyer in den Regelbetrieb gehen und die Strecke zwischen dem größten teilautomatisierten Logistikzentrum für Textilien in Norddeutschland und Kunden in Berlin weiter beackern wird. Außerdem gibt es Pläne zur Ergänzung der drei Wechselstationen um Schnelllademöglichkeiten. Zurzeit handelt es sich lediglich um die Erprobung eines Konzepts, klar ist aber auch: „RouteCharge“ zeigt, dass Dispositionsfreiheit kein Alleinstellungsmerkmal von Diesel-Lkw sein muss.
Herr Dr. Haskamp, auf der letzten Meile und in der Stückgut-Logistik haben wir E-Lkw schon erlebt. Sie sind mit „RouteCharge“ nun die Erschließung mittlerer Distanzen angegangen. In Ihrem Testaufbau konkret 250 Kilometer. Das kann nicht am Stück funktionieren, oder?
Aus statischen Gründen können nicht beliebig große Batterien am Fahrzeug befestigt werden. Außerdem muss das Verhältnis von Eigengewicht zu Nutzlast in Betracht gezogen werden. Derzeit sind nach unseren Erfahrungen 200 Kilometer mit einem Batterie-elektrisch betriebenen 19-Tonner Motorfahrzeug plus Anhänger möglich. Wir wollten explizit die „mittlere“ Distanz von 250 Kilometer im Praxistest erproben und haben dafür ein Batteriewechselsystem entwickelt.
Batteriewechselsysteme, die es aus dem Test- in den Regelbetrieb geschafft haben, kennen wir bisher vor allem von Anwendungen in der Mikromobilität. Etwa bei Swobbee in Berlin. Die Batteriekoffer wiegen da knapp zehn Kilogramm. Bei Ihnen kommen die zwei Batterieblöcke für den E-Lkw auf vier Tonnen. Warum soll dieser Technologieansatz gerade bei schweren Lkw sinnvoll sein?
Schwere Fahrzeuge benötigen im Verhältnis größere und damit schwerere Batterien, das ist richtig. Die Ladedauer von großen Batterien – in unserem Fall über 300 kWh – ist relativ lang. Die derzeitig für uns verfügbaren Ladestationen liefern maximal 80 kW, das heißt wir müssten drei Stunden an der Ladesäule stehen, um 240 kWh nachzuladen. Ein Batteriewechsel mit dem von uns entwickelten System ist unter 15 Minuten durchführbar.
Wenn man den Ansatz von „RouteCharge“ weiterdenkt, bräuchte man nicht nur viele Wechselstationen, sondern auch standardisierte Batteriekoffer für bestenfalls unterschiedliche Lkw-Marken. Wie aufwendig war die Modifizierung Ihres Testfahrzeugs?
Da haben Sie völlig recht. Mit unserem „RouteCharge“-Projekt zeigen wir die Machbarkeit. Wir werden das Fahrzeug auf der Route Berlin – Peine im Pendelverkehr in der Praxis erproben. Wenn es zum Beispiel auf der Route Berlin bis Dortmund entlang der A2 mehrere Wechselstationen gäbe, dann könnte das Fahrzeug auch auf dieser Langstrecke eingesetzt werden. Wenn unsere Batterie ein Quasi-Standard und damit offen für viele unterschiedliche Lkw werden könnte, dann wären wir natürlich sehr glücklich. Uns ist allerdings klar, dass wir nur einen ersten Impuls geben können. Eine Standardisierung und Industrialisierung des Batteriewechselsystems bedarf der Mitwirkung der Fahrzeugindustrie. Die Entwicklung und Herstellung des Fahrzeugs und des Batteriesystems dauerten circa zwei Jahre.
Die Kosten des Gesamtprojektes möchte ich hier nicht nennen. Jedoch können Sie davon ausgehen, dass man – ohne Infrastrukturinvestition – im günstigsten Fall von den dreifachen Kosten eines Diesel-Lkw ausgehen kann. Vergleichen Sie zum Beispiel, was ein E-Lkw aus der MAN-Kleinserie kostet. Unser in Manufakturbauweise hergestellter E-Lkw mit bewährtem Fahrgestell war naturgemäß viel teurer.
Wir haben nicht genau nachgezählt, aber im Erklärvideo zu Ihrem Projekt fallen sehr häufig die Schlüsselbegriffe „Sonderkonstruktion“ und „speziell entwickelt“ – was haben Sie konkret alles erfinden und konstruieren müssen, damit der Batteriewechsel funktioniert?
Ich nenne nur einige Stichworte:
- Umbau eines Diesel-Lkw zu einem E-Lkw mit Wechselbatterie
- Entwicklung einer fahrzeugseitigen Halterung, die einen Wechsel des Batteriesystem ermöglicht
- Entwicklung eines straßenverkehrstauglichen Steckersystems mit am Markt verfügbaren Komponenten für die elektrische Verbindung zum Fahrzeug und zur Batteriewechsel- /Ladestation
- Beschaffung und Anpassung batterieleistungsangepasster Gleich- und Wechselrichter in der Hochvolt-Trafostation
- Entwicklung eines Steuerungssystems für energieoptimiertes Laden und Erbringung von Regelleistung für Primärenergie
- Schaffung eines Zugangs zum Hochvoltnetz, um Schnellladung zu ermöglichen
- Entwicklung von Prognoseinstrumenten für Energieverbrauch und routenangepasste Ladeszenarien
- Bau einer Vorrichtung für das sichere Wechseln einer zwei Tonnen schweren Batterie und das Gegenstück der Fahrzeughalterung in der Ladestation
- Bau eines Schaltschrankes für die Steuerung des elektrischen Ladeprozesses. Diese emuliert in der stationären Ladestation die im Fahrzeug vorhandenen Sicherheitssysteme
- Errichtung einer speziellen Halle, in der alle Vorgänge des Batteriewechsels ausgiebig am Fahrzeug und am Wechselsystem getestet werden können
- Entwicklung und Bau eines Batteriewechselcontainers mit eingebautem Ladegerät für den Einsatz an externen Wechselorten
Kommen wir zur intelligenten Ladesteuerung, die dafür verantwortlich ist, dass immer eine aufgeladene Batterie zur Verfügung steht, wenn der E-Lkw eintrifft. Sie sorgt auch für Netzstabilität. Können Sie uns das erläutern?
Die Transport-Disposition des Lkw ist angehalten, den Einsatz des Fahrzeugs exakt zu planen. Die Daten werden in eine Software zur Planung des Batterieladezustands übernommen und ständig getrackt. Die benötigte Menge an elektrischer Energie wird dem Energieversorger zeitgenau vorhergesagt. Danach besorgt dieser die elektrische Leistung passgenau zum bestmöglichen Marktpreis für die Batterieladung. Dazu wird die Batterie unter anderem bei Überfrequenz geladen und unterstützt damit die Netzstabilität. Wir haben ein 50-Hz-Stromnetz und Netzbetreiber sind verpflichtet, diesen Wert exakt einzuhalten. Die Batterie kann in Sekundenbruchteilen überschüssige Energie aufnehmen und auch abgeben. Sie ist daher ein sehr guter Netzstabilisator. Insgesamt sind wir in der Lage, drei Wechselbatterien mit zusammen über 1 MW Leistung bereitzustellen.
Untersucht wurden vor diesem Hintergrund die Einsparpotenziale des Batteriewechsels durch das Dual-Use-Prinzip. Was können Sie uns dazu sagen?
„Dual-Use“ heißt bei uns, dass die Batterie zum einen als Speicher für Antriebsenergie genutzt wird und zum anderen als Speicher für überschüssige Netzenergie eingesetzt wird. Das hängt davon ab, ob sie sich gerade im Lkw oder in der Batteriewechselstation befindet. Die Wirtschaftlichkeit der Wechselbatterie wird dadurch verbessert, dass überschüssige Energie, zum Beispiel zu hohe PV-Leistung oder Windkraftleistung im Netz abgenommen wird. Der Energiepreis ist im Prinzip ein Börsenpreis, der sich nach der jeweiligen Verfügbarkeit richtet und genau dieses testen wir auch in unserem Projekt.
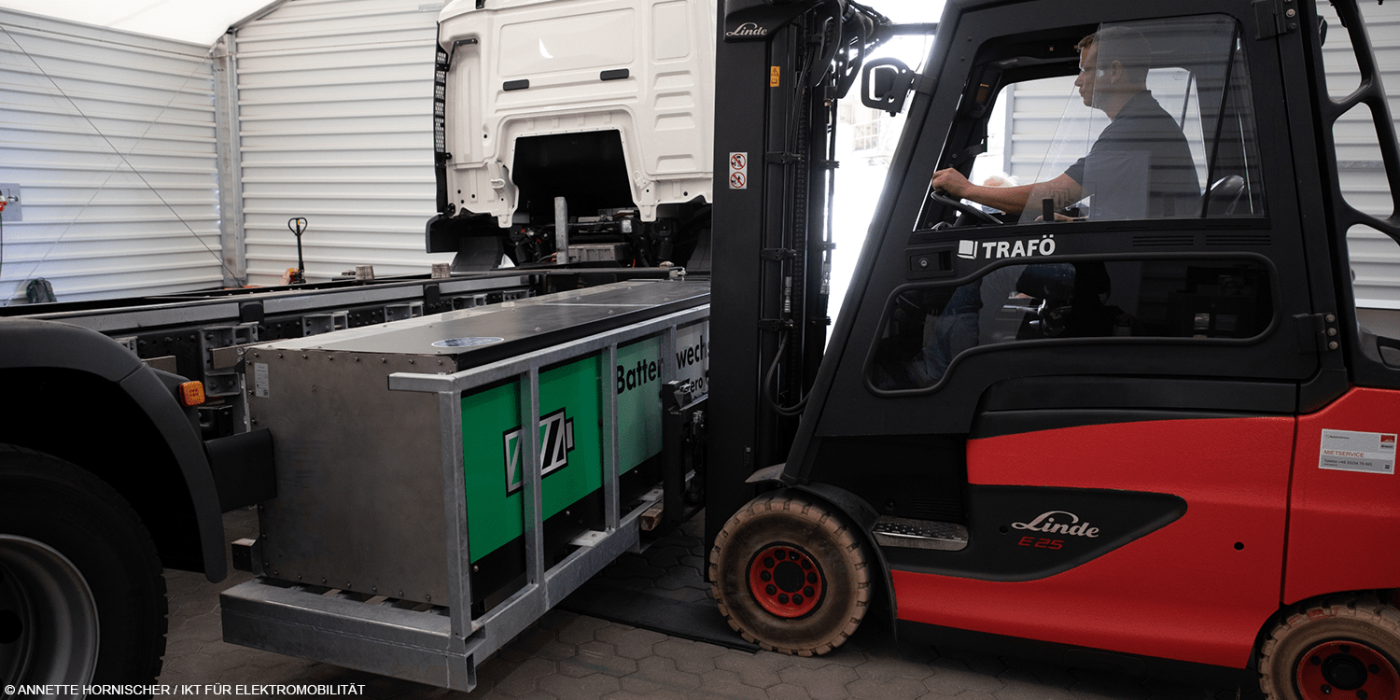
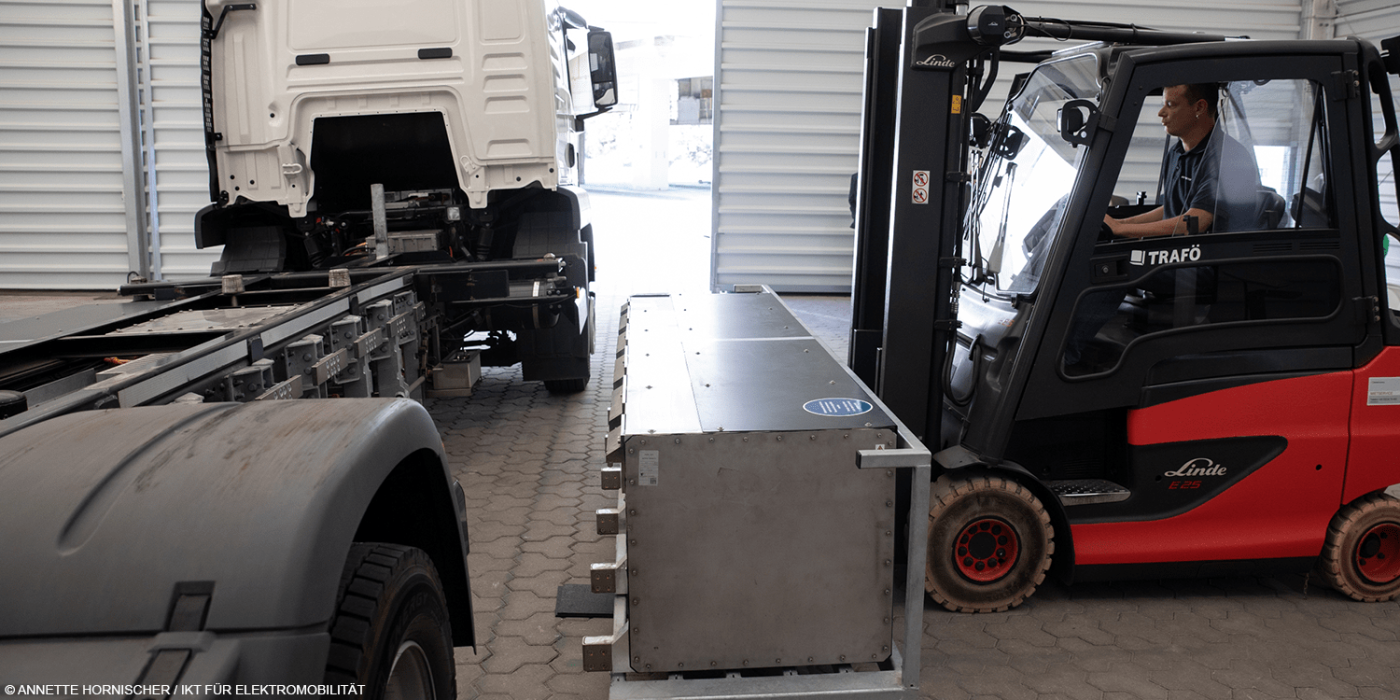
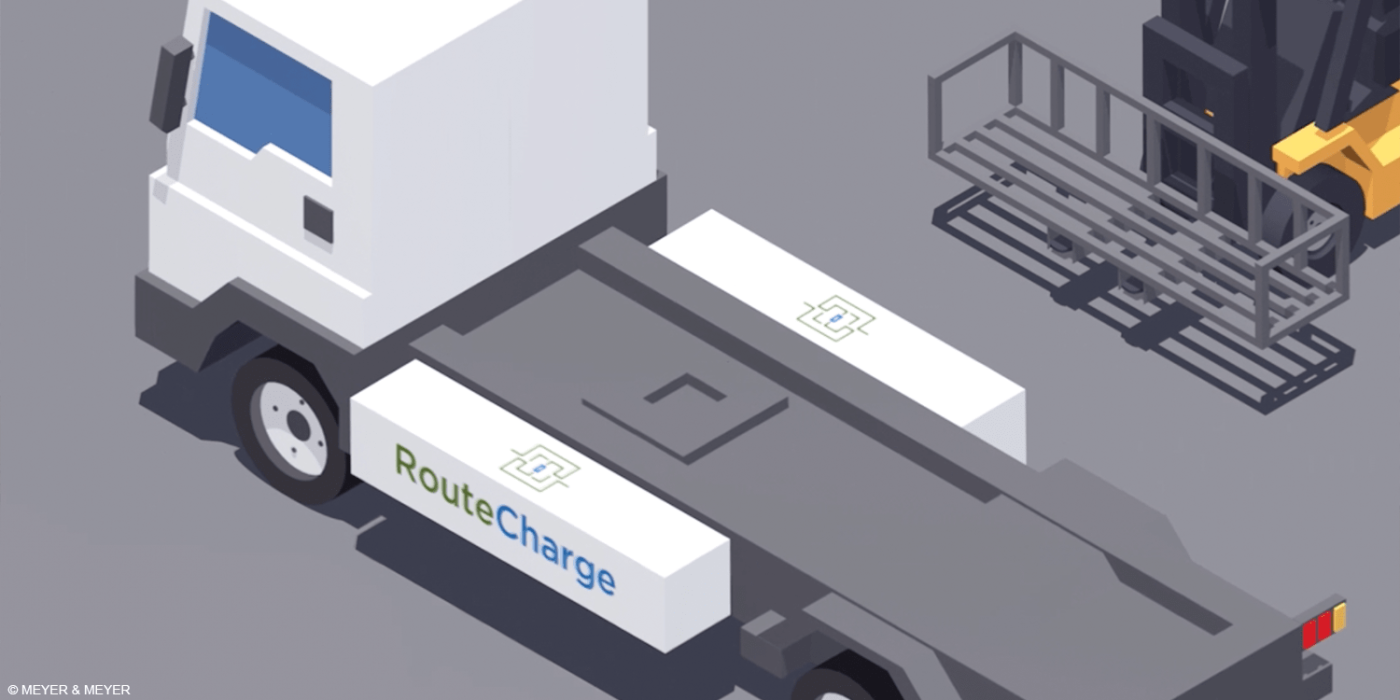
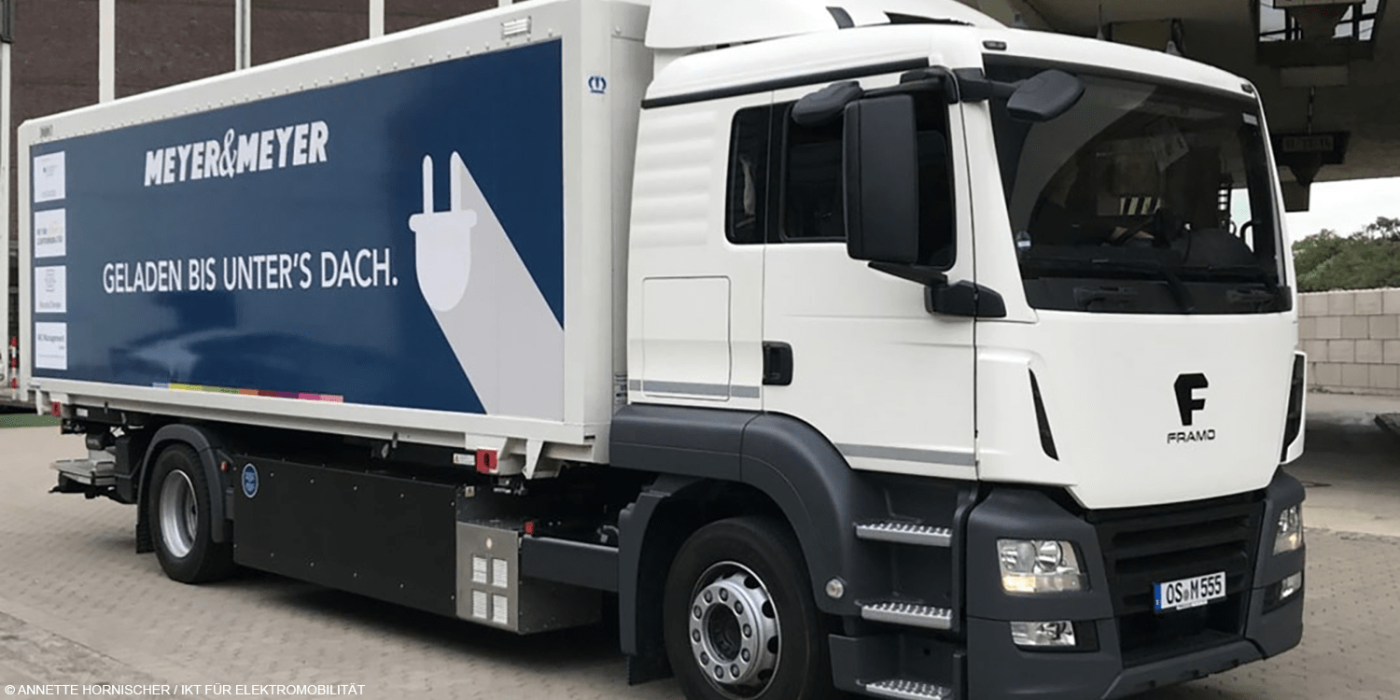
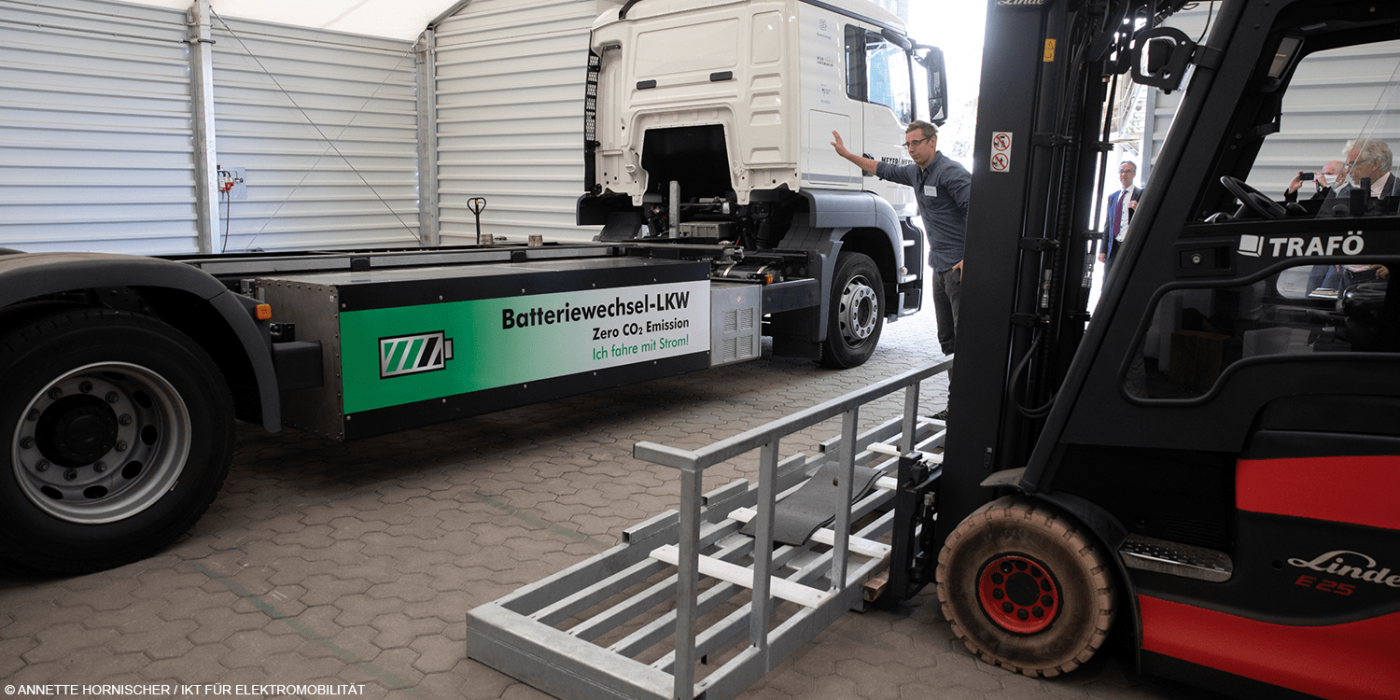
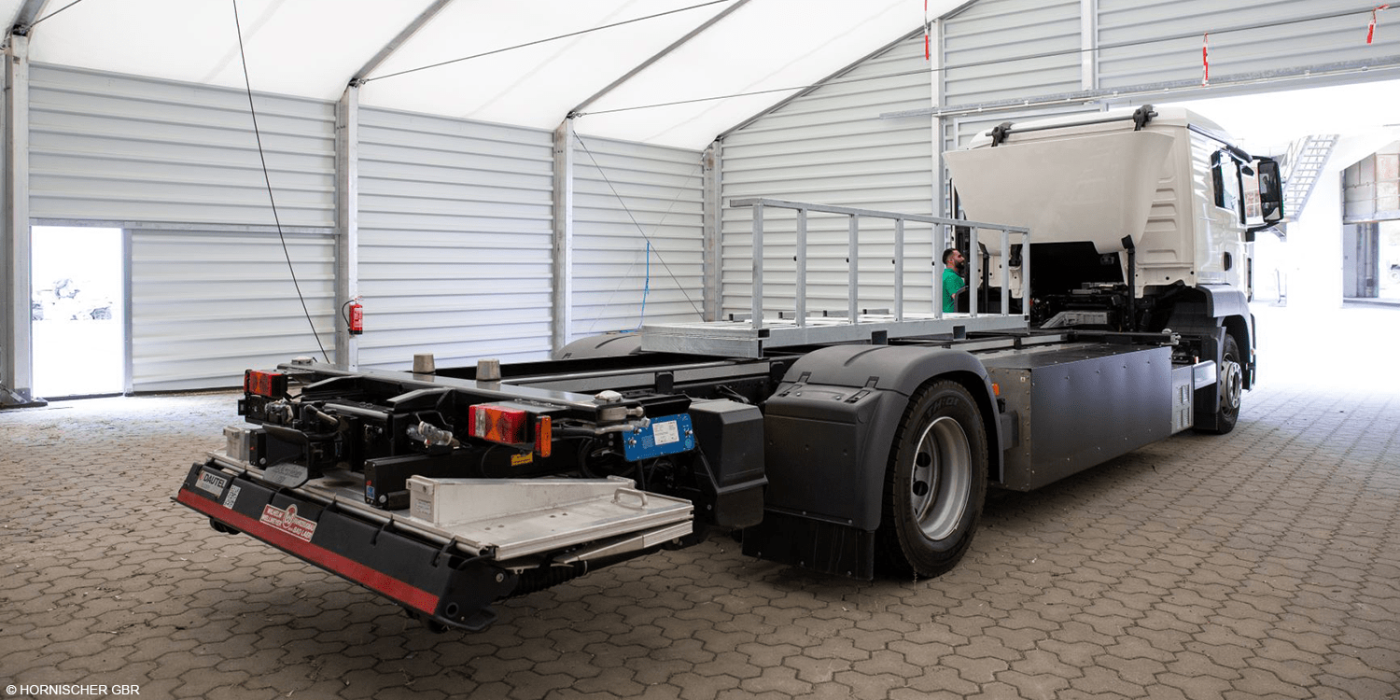
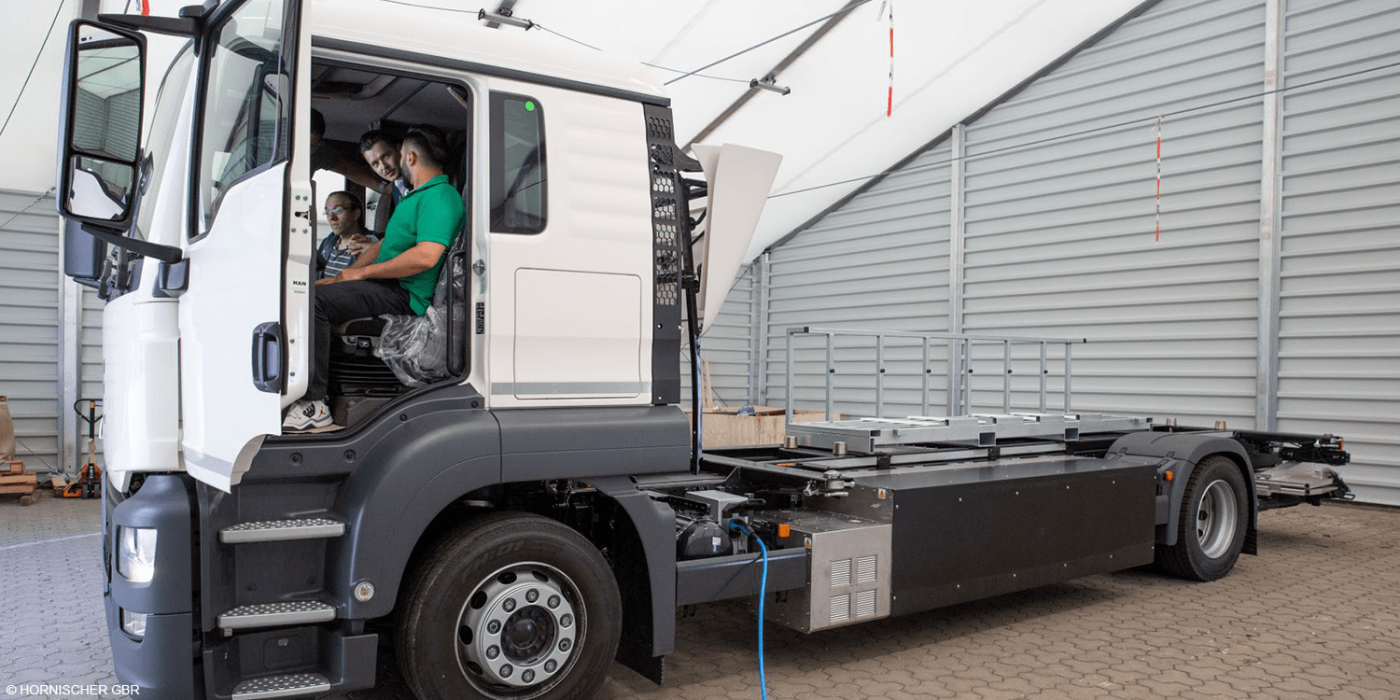
Und noch mal zurück auf die Straße: Hat Ihr Test-Lkw eigentlich schon mal im Stau gestanden? Ab welchen Batterieladestand wird der Fahrer nervös? Und wie steht es um die Sicherheit des Fahrers bei einem Unfall?
In einem „richtigen“ Stau hat der Test-Lkw noch nicht gestanden, nur die üblichen Ampelstaus. Der Vorteil eines E-Lkw ist, dass er im Stillstand so gut wie keine Energie benötigt. Das Anfahren lässt die Anzeigenadel jedoch stark ausschlagen. Wir fahren unser Test-Fahrzeug nicht auf den niedrigsten Ladezustand herunter. Bei maximal 20% SoC wird nachgeladen. Die im Lkw vorhandene Software und Anzeige zur Reichweitenermittlung lässt den Fahrer so schnell nicht nervös werden. Er bekommt zeitig angezeigt, wann er nachladen sollte.
Zur Frage nach der Sicherheit: der Test-Lkw ist von einem zertifizierten Prüfunternehmen nach den aktuellen Regeln der Verkehrssicherheit abgenommen worden. Die Batterien sind gut geschützt. Das Fahrzeug ist mit allerlei Kontroll- und Sicherheitssystemen ausgerüstet. Wir erkennen daher keine außergewöhnliche zusätzliche Gefahr für den Fahrer durch den Einsatz des batterieelektrisch angetriebenen Lkw.
Interessant ist natürlich, ob Elektro-Lkw mit Batteriewechselvorrichtung in puncto Flexibilität mit konventionellen Lkw mithalten können. Wie lautet da Ihr Fazit?
Na ja, nach dem ersten Anschein ist ein mit fossiler Energie betankter Lkw sicherlich flexibler als ein Batterie-elektrisch betriebener Lkw: Volltanken, Schlüssel umdrehen und losfahren. Der Betrieb eines E-Lkw mit Wechselbatterie verlangt eine intelligente Steuerung. Das haben wir ausgiebig getestet. Dann kann er durchaus in der Flexibilität mit einem konventionellen Lkw beziehungsweise Transportsystem mithalten. Planung ist die halbe Miete. Darüber hinaus gibt es vielfältige Einsatzbereiche, in denen der E-Lkw auch mehr Flexibilität bieten kann, zum Beispiel bei lärmarmen Transportanforderungen, beim Nachtbetrieb in der Innenstadt und dergleichen sowie natürlich auch beim emissionslosen Fahren. Das kann ein konventioneller Lkw nämlich definitiv nicht.
Eine Kombination von Oberleitung und Batterie, auf der Langstrecke am Netz fahren und auf der Kurzstrecke mit Batterie, das wäre sicherlich dauerhaft ein sehr sinnvoller Ansatz, um fossile Energie einzusparen und gute Flexibilität für elektrisch betriebene Lkw zu erhalten.
Im Feldversuch läuft das Projekt „RouteCharge“ noch bis Ende 2020. Was passiert danach mit den drei Wechselstationen und dem modifizierten 19-Tonner? Werden sie weiterhin genutzt?
Nach Projektende ist geplant, dass der E-Lkw durch das international tätige Transport- und Logistikunternehmen Meyer & Meyer im Echteinsatz auf der Pendelstrecke Berlin – Peine genutzt wird. Seinen Nutzen wird das E-Fahrzeugsystem insbesondere durch seine Fähigkeit beweisen, dass es als wohl einziges oder zumindest einzigartiges Fahrzeug mit Anhängerbetrieb genutzt werden kann. Ein E-Lkw im Schwerlastbereich mit Anhänger, das halten wir schon für etwas Besonderes. Die Wechselstationen sollen dementsprechend auch weitergenutzt und sogar noch ausgebaut werden. Wir planen, dass an den Wechselstationen Schnellademöglichkeiten AC-AC (Gleichstromladen) für die gängigen Ladestecker geschaffen werden. So können dort aus den Batterien heraus dann auch E-Pkw oder auch E-Transporter oder E-Lkw mit hoher Geschwindigkeit geladen werden. Das ist unser Ziel. Vielleicht haben wir aber auch Interesse geweckt und es finden sich Industriepartner für eine Verwertung der Erkenntnisse aus „RouteCharge“ in größerem Stil.
Herr Dr. Haskamp, haben Sie vielen Dank.
Über das Projekt:
„RouteCharge“ ist ein gemeinschaftliches Projekt des Technologieprogramms „IKT für Elektromobilität“ mit einer zwischenzeitlich verlängerten Laufzeit von Frühjahr 2016 bis Ende 2020. Es wird vom Bundesministerium für Wirtschaft und Energie gefördert. Zum Konsortium gehören federführend die MC Management GmbH sowie die WEMAG AG, die TU Berlin, das DAI-Labor und das Fraunhofer IPK. Gegenstand des Projekts ist die Realisierung eines Batteriewechselsystems für die Erschließung mittlerer Distanzen bei der Filialbelieferung mit E-Nutzfahrzeugen.
0 Kommentare