electrive LIVE: Wie sieht der E-Antrieb der Zukunft aus?
In der „alten“ Autobranche galten Elektromotoren lange Zeit – wie auch die Tranktionsbatterie – als Zulieferteil. Und in der Tat haben viele Hersteller bei der ersten Generation ihrer E-Autos auf zugekaufte E-Motoren von ZF, Vitesco, Bosch, Siemens, Valeo & Co gesetzt. Diese Maschinen waren mit überschaubarem Aufwand verfügbar, das Investitionsrisiko ohne eigene Produktion gering. Schließlich war man sich lange Zeit in den Chefetagen noch nicht so sicher, was das mit diesen Elektroautos überhaupt wird.
Einige Jahre später ist die Lage einen andere: Lokal emissionsfreie Antriebe sind für die Branche der Weg in die Zukunft. Zulieferer entwickeln ihre Elektromotoren von starren Konstruktionen zu modularen Baukästen weiter, damit die OEM nicht nur die Antriebe für ihre Bedarfe konfigurieren können, sondern auch ihren Kunden mehr als den „Einheitsbrei“ mit den immer gleichen, technischen Daten anbieten können. Andere OEM nehmen Entwicklung und Produktion der E-Motoren inzwischen selbst in die Hand – so können individuelles Design und wettbewerbsdifferenzierende Lösungen entwickelt werden. Und auch Jobs in der Produktion bleiben erhalten.
Klar ist: Es ist eine spannende Phase der Entwicklung. Es müssen neues Knowhow erarbeitet und Lieferketten etabliert werden. Statt Kolbenringen und Einspritzdüsen müssen nun Permanentmagnete und Leistungselektroniken eingekauft werden. Und bei der Entwicklung geht es nicht nur um das Spannungsfeld zwischen Kosten und Performance, sondern das Produkt soll auch möglichst nachhaltig sein. Anlass für uns von electrive, das Thema mit Experten und 450 digitalen Gästen per Online-Konferenz zu diskutieren.
Breites Antriebsportfolio bei Volkswagen
Den Anfang bei der 34. Ausgabe von electrive LIVE macht Alexander Krick, Leiter der Entwicklung E-Antrieb, Leistungselektronik & Getriebe bei der Volkswagen AG. In seinem Videobetrag stellt Krick die Strategie zur Elektrifizierung des Antriebsstrangs der Wolfsburger vor – und zwar nicht nur jene der Marke, sondern die Strategie des gesamten Volkswagen-Konzerns. Denn Kricks Stelle selbst ist bei der Volkswagen Group Components angesiedelt.
Für seine E-Autos hat der Konzern derzeit den MEB auf dem Markt, die PPE als „Premium Plattform Electric“ steht mit dem Porsche Macan und Audi Q6 e-tron kurz vor dem Marktdebüt. In der Entwicklung blickt Krick aber schon weiter: Beide Plattformen sollen zur SSP, der „Scalable Systems Platform“, weiterentwickelt und zusammengefasst werden – also einer umfassenden Plattform für alle E-Autos des Konzerns, vom Kleinwagen bis in die Oberklasse und zu den Sportwagen.
„Hierfür entwickeln wir ein Antriebs-Portfolio, das allen Marken gerecht wird“, sagt Krick. Die Aufgabe ist groß: Schließlich muss der Antriebsbaukasten vom preiswerten Fronttriebler bis zum komfort- oder leistungsorientierten Allradler alles abdecken können – mit dem Mittelklasse-Hecktriebler dazwischen. Mal stehen die Kosten im Fokus, mal die Leistungsdichte, mal die Effizienz. Der Ansatz von Kricks Team: Nichts wird ausgeschlossen. Für die SSP plant VW mit Asynchronmotoren, permanenterregten Synchonmotoren und auch fremderregten Synchronmotoren.
Und: Künftig werden auch die Inverter bzw. Pulswechselrichter hausintern entwickelt – konkret im Standort Kassel. „Der Inverter ist maßgeblich für die beste Effizienz und Performance verantwortlich“, erklärt Krick. „Daher entwickeln wir diese Komponente nicht nur auf Systemebene, sondern wir brechen das Gesamtsystem auf, indem wir bis auf die Ebene der Halbleiter heruntergehen.“ Die ersten Ergebnisse haben nicht nur zu mehreren Patenten auf Seite der Hardware geführt, sondern auch zu patentierten Lösungen bei den Regel-Algorithmen.
Wie recycelt man eine E-Achse?
Im zweiten Vortrag kommt mit Thomas Triboulet ein Vertreter von Bosch zu Wort. Der Franzose stellt aber nicht die neuesten Entwicklungsergebnisse des Zulieferers beim Design der Rotoren oder dem hochintegrierten Gesamtsystem vor. Triboulet ist Director Sustainability Powertrain Solutions bei der Robert Bosch GmbH – und damit für die Kreislaufwirtschaft verantwortlich.
Wie kann ein Elektroantrieb auf allen Ebenen nachhaltig werden? Diese Frage treibt Triboulet in seinem Arbeitsalltag um. Gemäß den Scope-1- und Scope-2-Kriterien ist Bosch selbst seit 2020 bilanziell CO2-neutral – wenn auch noch mit Hilfe von Zertifikaten, wie Triboulet einräumt. Deren Anteil sinke aber stetig. Doch Scope 1 und 2 erfassen nur die direkten Emissionen von Bosch selbst, was aber nur einen Bruchteil der Gesamtemissionen der Bosch-Produkte ausmacht, gemessen von der Rohstoffgewinnung (Scope 3 Upstream) bis hin zur Nutzungsphase, nachdem die Produkte die Werkshallen des Zulieferers verlassen haben (Scope 3 Downstream). Hier CO2-neutral zu werden, ist also der ungleich größere Hebel. Es ist aber auch mit deutlich größeren Herausforderungen verbunden.
Um die Aufgaben zu veranschaulichen, kommt Triboulet doch auf die eAchse des Zulieferers zu sprechen. Diese besteht aus rund 100 Kilogramm Stahl, Aluminium, Kupfer, Magneten und diversen Kunststoffen. Um die eAchse nachhaltiger zu machen, kann in der Entwicklung der Einsatz von Kupfer und Magneten reduziert werden. Zudem wird der ganze Antrieb wartungsfrei konzipiert. Und wird dennoch eine Komponente beschädigt, gibt es Reparaturkonzepte, anstatt die ganze eAchse zu tauschen. All das hat Bosch selbst in der Hand.
Geht es dann aber nach der Nutzung an das Recycling, stelle man laut dem Bosch-Experten schnell fest, dass die Materialkreisläufe eben noch nicht geschlossen sind. Ein Beispiel: Das Alu-Guss-Gehäuse der eAchse besteht bereits heute zu einem großen Anteil aus Recyclat. Nur handelt es sich dabei nicht um altes Aluminium aus der Autoindustrie, sondern aus der Getränkebranche. „Wir sind darauf angewiesen, dass Sie Softdrinks und Bier aus Dosen trinken“, scherzt Triboulet. „Im Ernst: Wir sind auf die Getränkeindustrie angewiesen. Sobald die Getränkeindustrie selbst ihre Rohstoffe umstellt oder zurückgewinnt, haben wir ein Problem.“
Was er meint: Für die eAchsen gibt es kein Pfand- oder Rückgabesystem. Der E-Antrieb wird gemeinsam mit dem ganzen Auto geschreddert, die Späne dann sortiert. Selbst wenn dort das Aluminium herausgefiltert werden kann, sind in den Spänen unzählige Alu-Legierungen gemischt. Damit kann man nur noch minderwertige Produkte herstellen, für das Gehäuse einer eAchse ist diese Alu-Mischung nicht geeignet. Man könnte sie nur in gewissen Mengen reinem Aluminium beimischen – doch dann fallen bei der Schmelze wieder CO2-Emissionen an. Für derartige Analysen arbeitet Bosch übrigens mit dem „Circular Navigator“ der Universität St. Gallen.
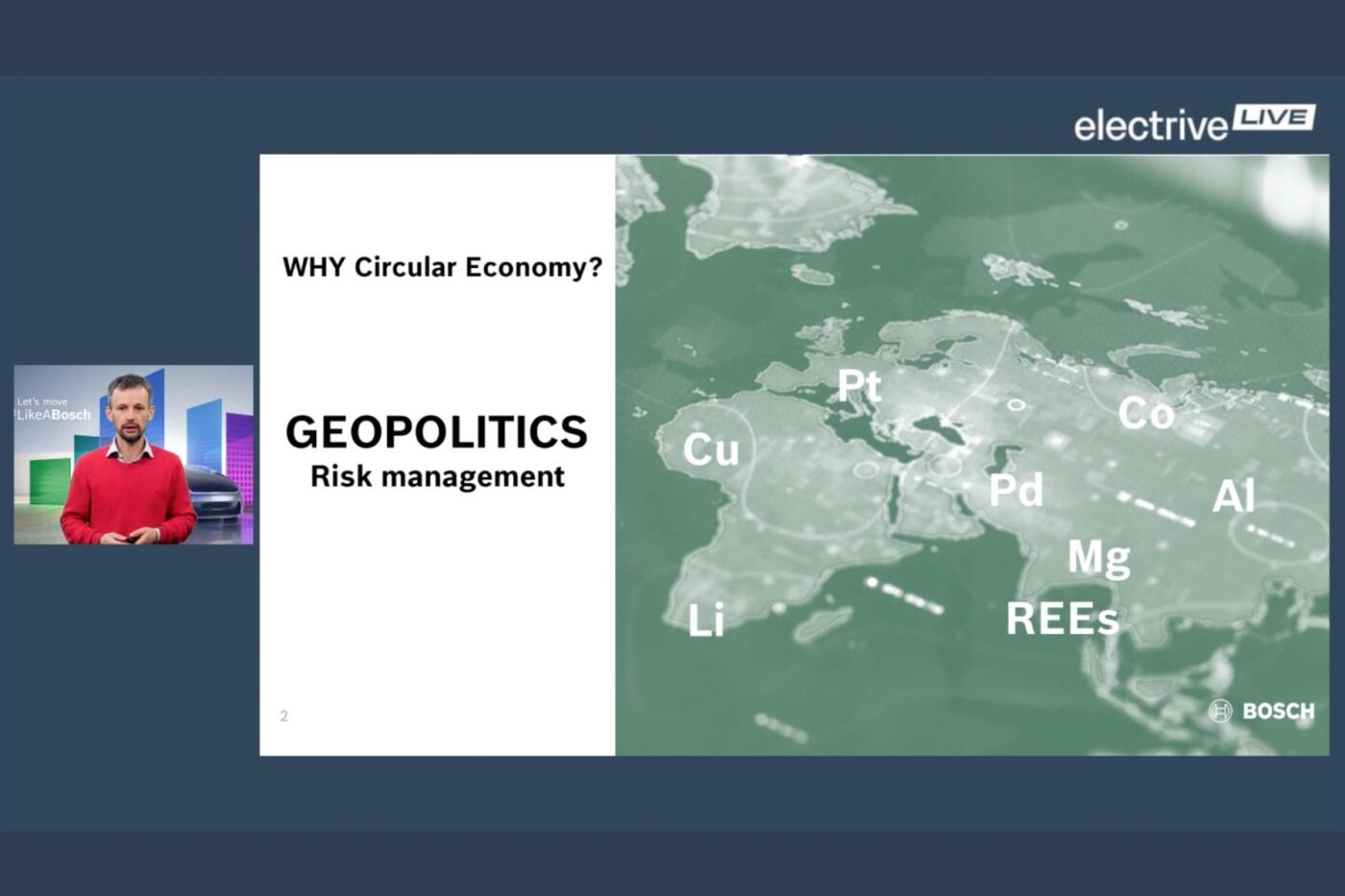
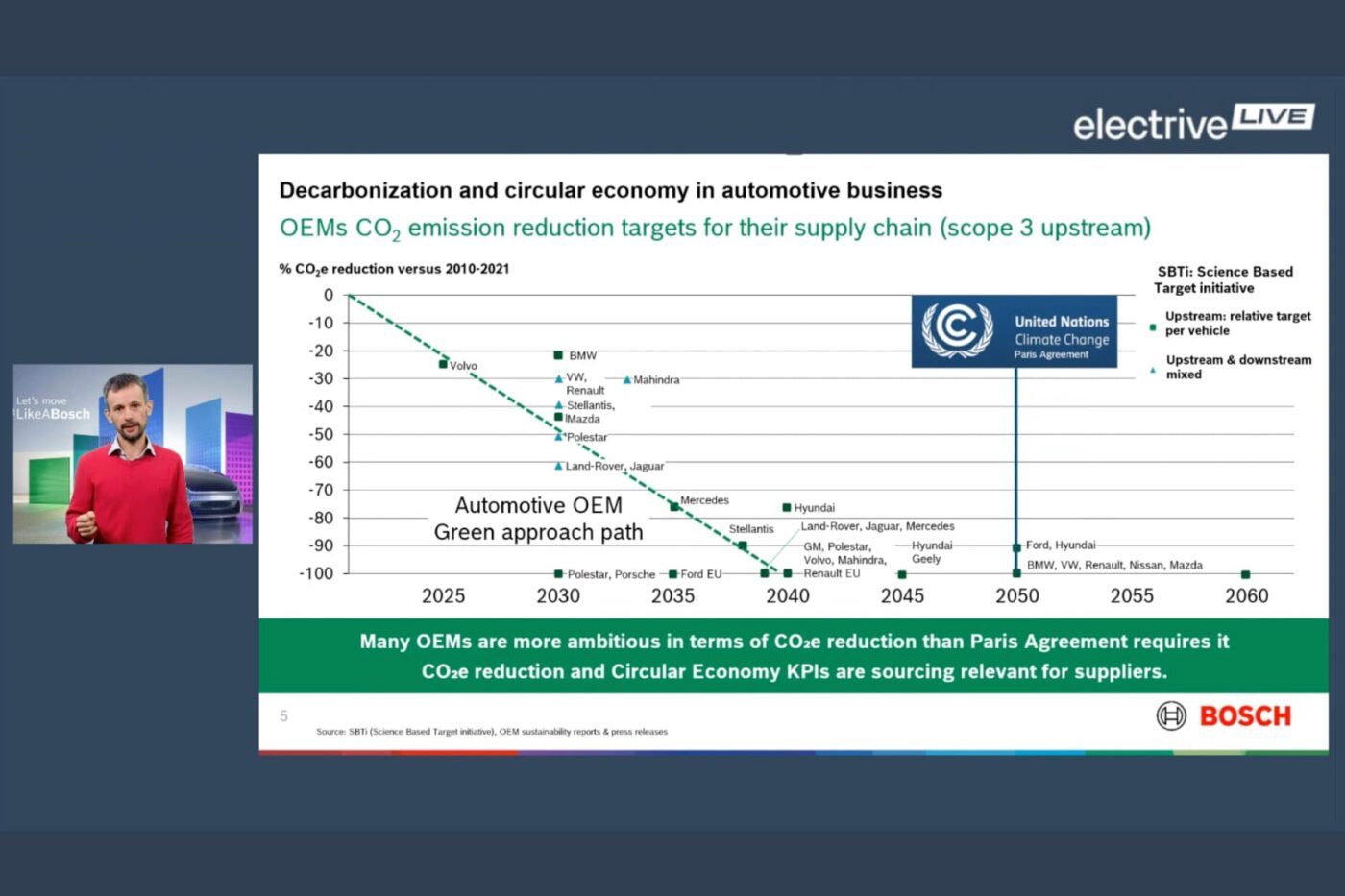
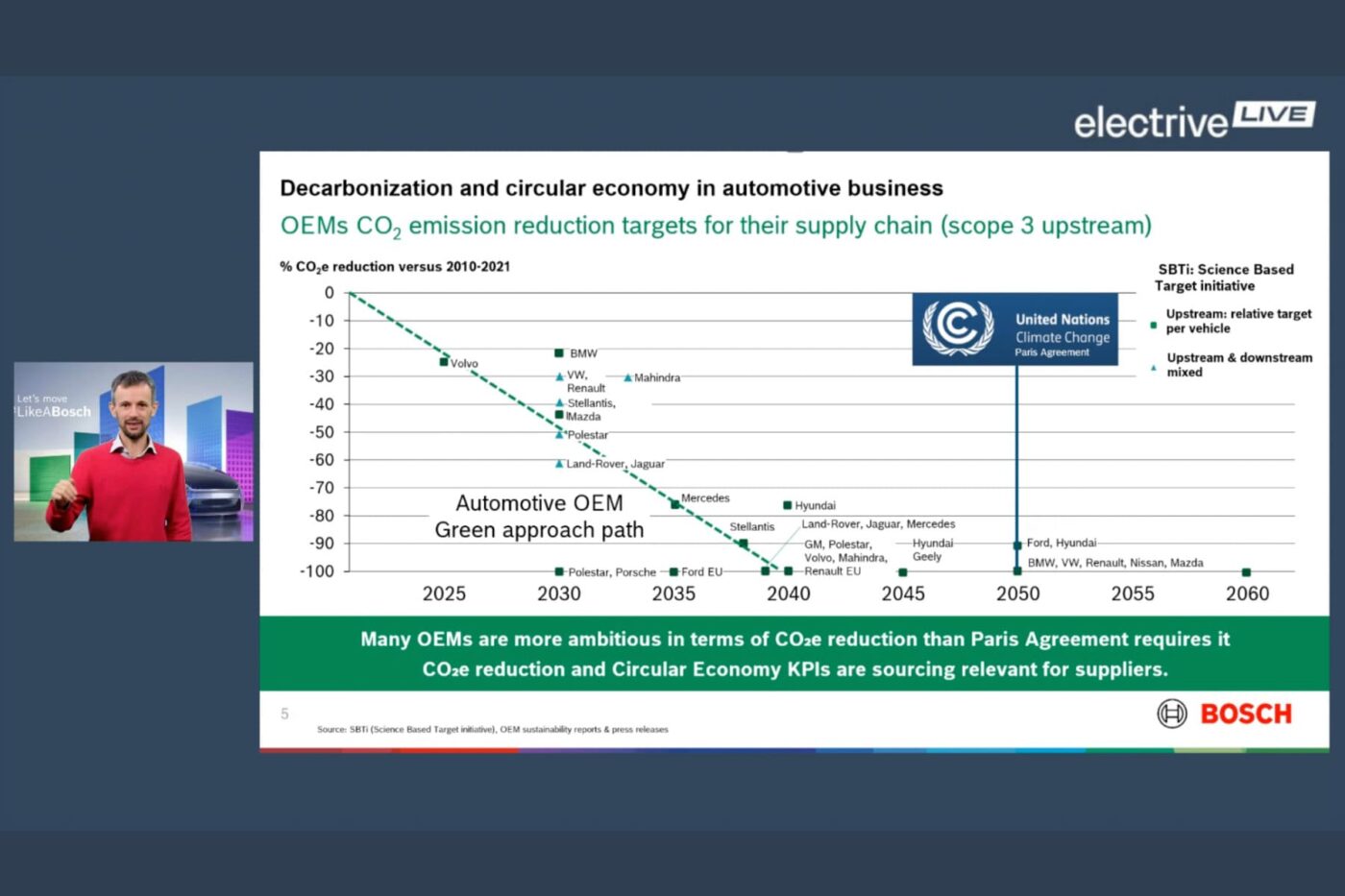
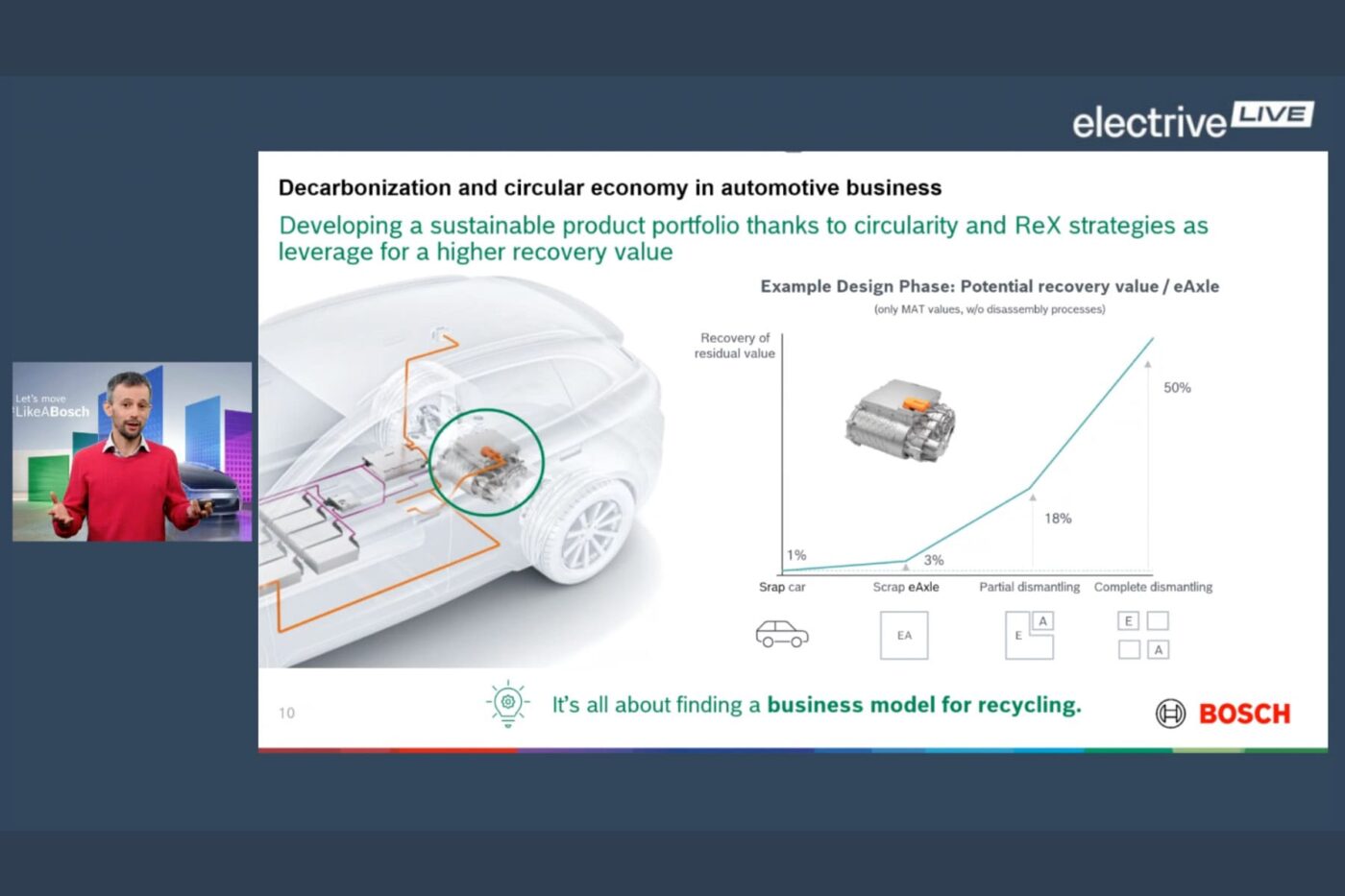
Ein Ergebnis ist, dass mit einer Demontage der eAchse bis zu 50 Prozent recycelt werden könnten. Doch in der Praxis kommen Zulieferer nicht so einfach an ihre Bauteile, nachdem sie an den OEM geliefert wurden – und dieser die verbaute Komponente an den Endkunden verkauft hat. „Die Produktrücknahme ist ein zentrales Hindernis für die Kreislaufwirtschaft“, sagt Triboulet. „Hier untersuchen wir verschiedene Konzepte von der Miete oder ein Vorkaufsrecht.“ In einem Pilotversuch hat Bosch etwa eine Partnerschaft mit dem BZ-Lkw-Vermieter Hylane geschlossen: Bosch hat ein Vorkaufsrecht für die Brennstoffzellen der Lkw, sobald sie außer Dienst gestellt werden. Der Zulieferer will dann das darin enthaltene Platin recyceln. Dieses Material habe dann bis zu 95 Prozent CO2 eingespart, wenn man den Platin-Abbau als Vergleichsgröße nimmt.
Weil die Hürde, an die ausgedienten Produkte zu kommen, so hoch ist, befürwortet Triboulet eine strengere Regulierung. „Die Batterieverordnung zwingt uns, den Kreislauf für die Batterien zu schließen“, gibt der Bosch-Experte ein Beispiel. „Solche Regelungen helfen uns, indem sie Standards schaffen, Wettbewerbsverzerrungen verringern und unsere Abhängigkeiten bei der Rohstoff-Beschaffung vermindern.“
Optimale Schmierung für mehr Effizienz
Recycling ist ein Weg, E-Antriebe nachhaltiger zu machen. Es ist aber auch wichtig, ihre Effizienz im Betrieb weiter zu verbessern, um so ihren Energieverbrauch in der Nutzungsphase zu senken. „Es besteht ein großes Einspartpotenzial, wenn durch weniger Reibung weniger Energie aufgewendet werden muss“, sagt unser dritter Speaker, Thomas Kraft. „Die Revolution ist definitiv vorbei, wir arbeiten jetzt an der Evolution des E-Motors.“
Kraft ist Business Development Manager E-Mobility bei der Fuchs Lubricants Germany GmbH – richtig gelesen, es geht um Schmierstoffe. Denn auch wenn ein Elektroauto keinen Ölwechsel mehr braucht: Geschmiert wird trotzdem!
Fuchs, 1931 in Mannheim gegründet und immer noch zu 55 Prozent in Hand der Familie, ist vielen zwar kein bekannter Name, aber immerhin der achtgrößte Schmierstoff-Hersteller der Welt – mit 35 Produktionsstandorten weltweit. Und ebenfalls wichtig: Fuchs betreibt auch Labore in 24 Ländern, recht genau ein Zehntel der 6.000 Angestellten arbeitet in der Forschung und Entwicklung.
Das eMobility-Portfolio hat Fuchs in verschiedene Bereiche aufgeteilt. Geht es um eine trockene Schmierung oder ein nasses System? Soll die Lösung gleichzeitig auch noch kühlen oder nicht? „Je nach Temperaturbereich und den weiteren Anforderungen ist dann eine unterschiedliche Formierung des Schmierstoffs nötig“, erklärt Kraft. Klar ist: Es geht in diesem Teil des Maschinenbaus längst nicht mehr nur darum, reine Aufgaben bei der Schmierung von Metall auf Metall zu übernehmen – sondern das Gesamtsystem zu optimieren.
„Unseren Kunden ist dabei sehr wichtig, dass die Schmierung die Effizienz verbessert“, so Kraft. „Ganz klar: Der Schutz vor Abnutzung, die Materialkompatibilität und die elektrischen Eigenschaften müssen auch den Anforderungen entsprechen, was wir in unseren Laboren auch alles sicherstellen können. Aber der Fokus liegt darauf, die Reibungsverluste zu verringern.“
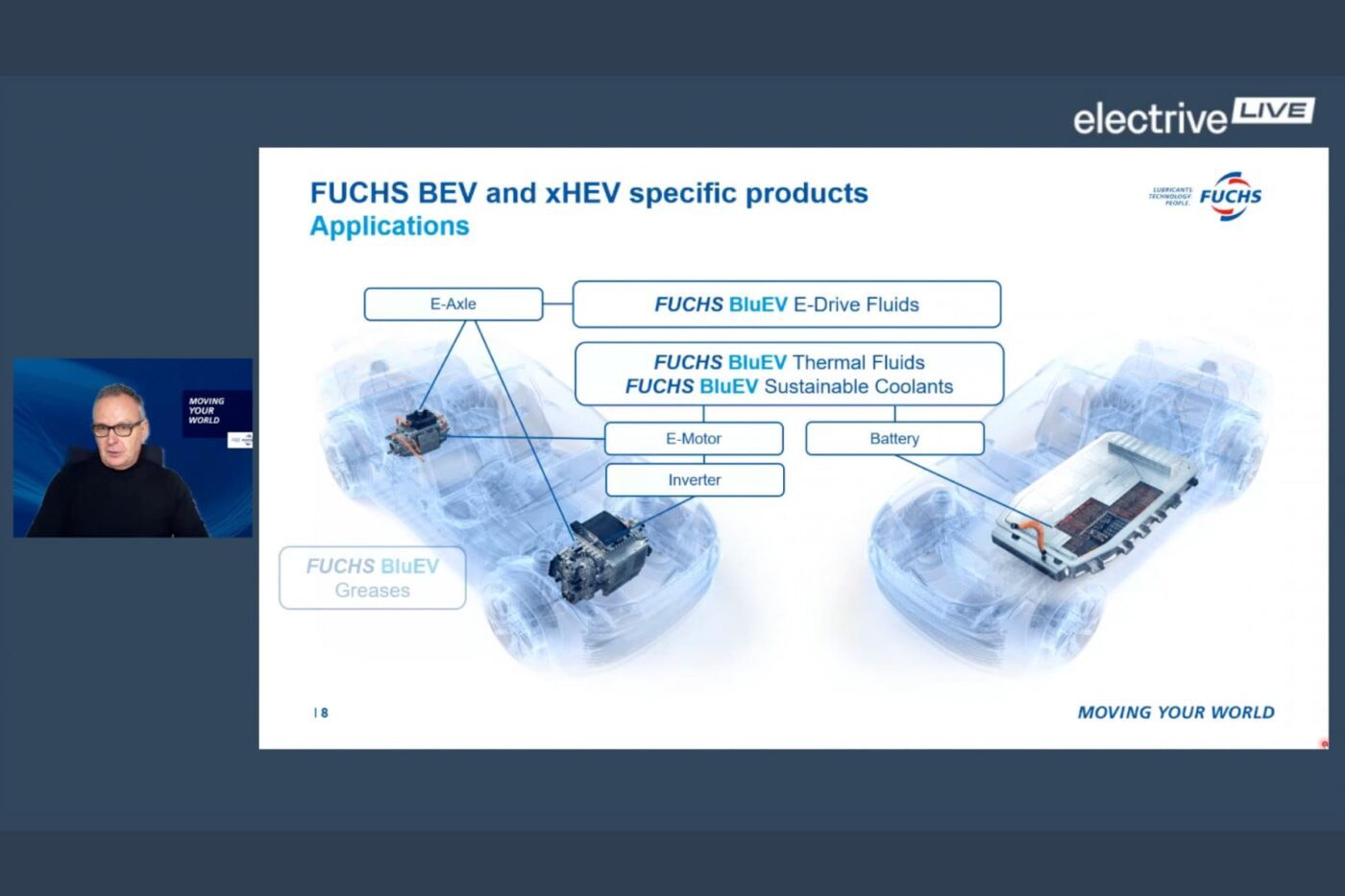
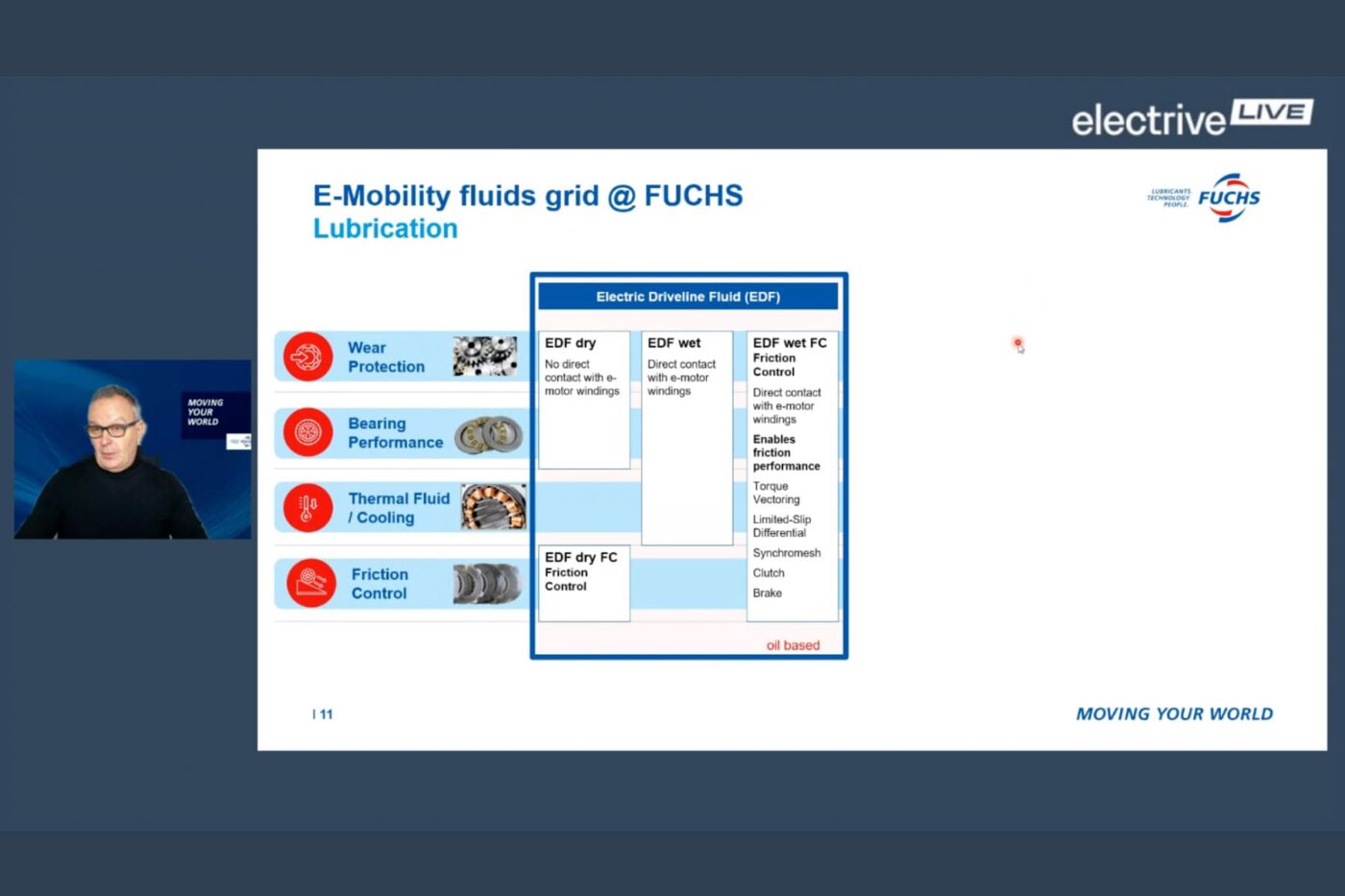
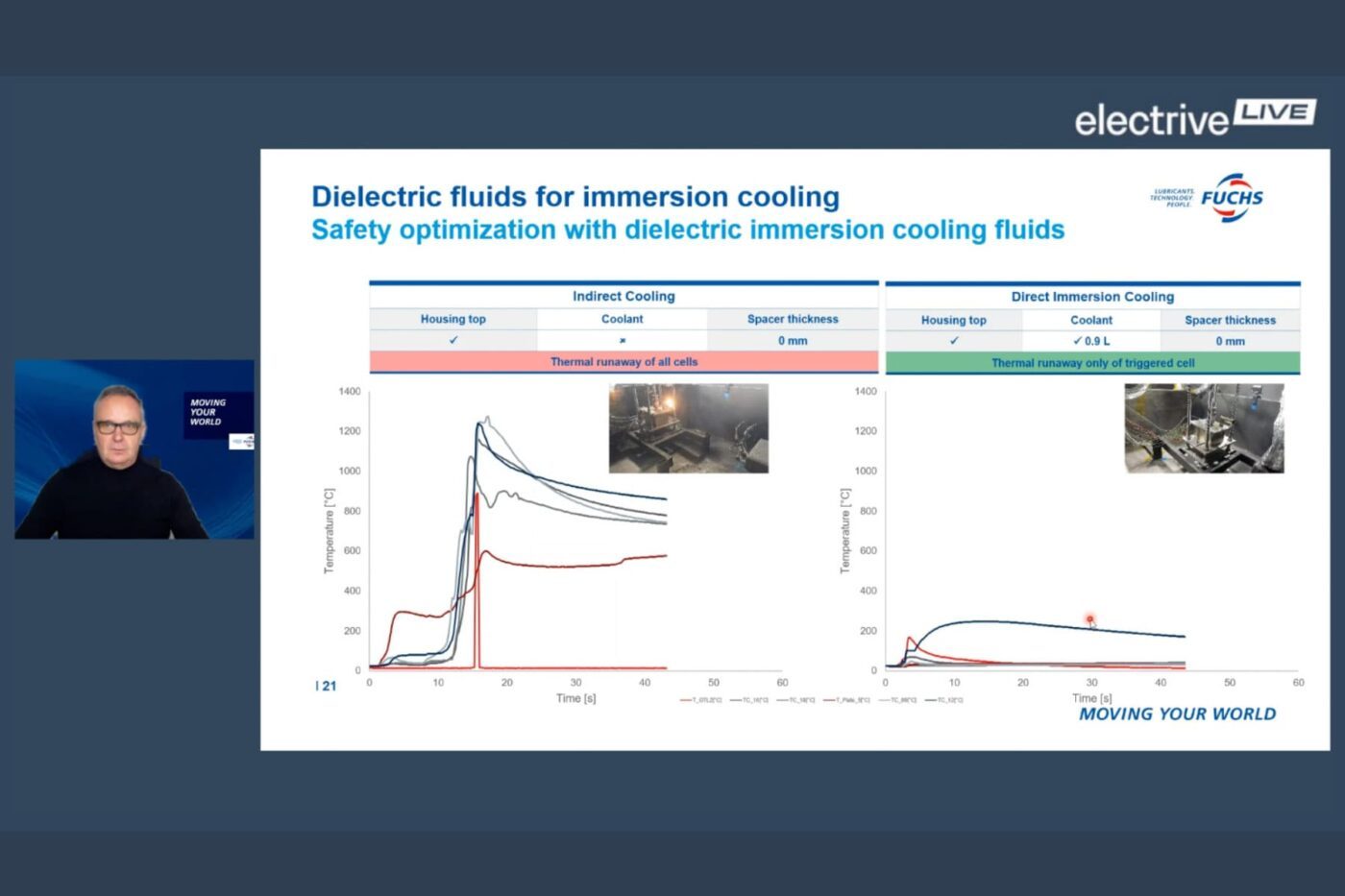
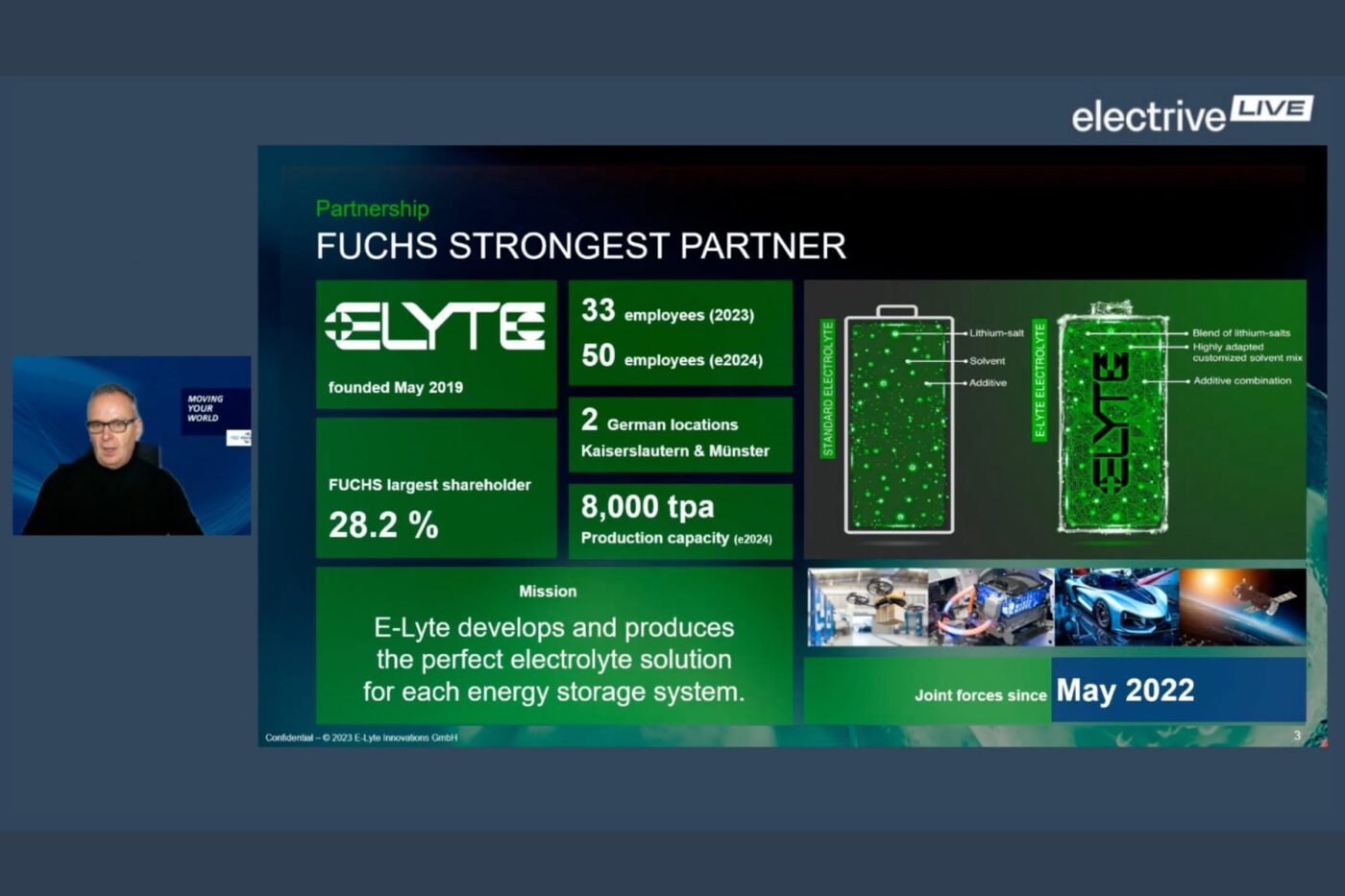
Bei Fuchs geht es aber nicht nur um die Kühlung der E-Antriebe und ob der Stator jetzt per Wassermantelkühlung mit einem wasserbasierten Fluid oder mit einer direkten Ölkühlung (und einem ölbasierten Fluid) gekühlt werden. Das Unternehmen hat sein Knowhow auch genutzt, um eigene Fluide für die Batteriekühlung zu entwickeln. Diese unterscheiden sich von den Kühlmitteln für die E-Motoren, weil diese am direkten Oberflächenkontakt deutlich heißer werden. Die Batterie bewegt sich in einem anderen Temperaturbereich.
In diesem Zuge hat Fuchs auch eine Batterie-Immersionskühlung erprobt, bei der die Kühlflüssigkeit nicht durch eine Kühlplatte am Boden des Batteriegehäuses fließt, sondern quasi das ganze Gehäuse füllt und die Zellen direkt umfließt. Das Potenzial ist groß, auch bei der Sicherheit: Fuchs führt Videos eines internen Tests vor, bei dem zwei vergleichbare Batteriepacks mit NCA-Rundzellen einem Nagelpenetrationstest unterzogen wurden. Bei der Variante ohne die Immersionskühlung gehen alle Zellen thermisch durch, es werden enorme Temperaturen erreicht. Mit der Immersionskühlung entzündet sich aber nur die eine Zelle, in die der Nagel eingeschossen wurde. Selbst die direkt angrenzenden Zellen werden so gekühlt, dass sie sich nicht entzünden.
Trotz dieser eindrucksvollen Demonstration sieht Kraft die Immersionskühlung „aufgrund der anspruchsvollen, technischen Umsetzung“ eher in High-End-Fahrzeugen. „Bei Volumenmodellen erwarten wir noch lange Zeit eine wasserbasierte Kühlung, die für den Temperaturbereich optimiert ist“, sagt Kraft. Aber auch dort gibt es noch Potenzial: Dank der höheren Wärmeleitfähigkeit im Vergleich zu einem Referenzprodukt werde etwa weniger Kühlfläche benötigt – und die CO2-Ersparnis beträgt laut Kraft bis zu 70 Prozent.
Weitere Ansätze, um die Schmierstoffe nachhaltiger zu machen: Wird die Lebensdauer weiter erhöht, müssen die Schmierstoffe noch seltener gewechselt, entsorgt und durch neue Schmierstoffe ersetzt werden. Und auch das Reycling bzw. die Aufarbeitung von Schmierstoffen wird erprobt. „Wir sind zwar nicht auf die Getränkeindustrie oder Bierdosen angewiesen, aber sehr wohl auf Lieferungen von Altöl, um diese wieder in Verkehr zu bringen“, sagt Kraft in Anspielung auf die Aussage von Bosch-Manager Triboulet.
Bei Fuchs geht es zwar primär um Schmierstoffe und Kühlung, aber dennoch blickt das Familienunternehmen auch über den Tellerrand. Die Mannheimer haben sich etwa an Elyte beteiligt, einem auf Batterie-Elektrolyte spezialisierten Spinoff der Universität Münster. Elyte verfügt über eine eigene Produktion in Kaiserslautern, wo 8.000 Tonnen pro Jahr hergestellt werden können – laut Kraft das einzige Werk für Elektrolyte in Europa. Eine Parallele zum Kerngeschäft von Fuchs gibt es: „Es gibt kein Universal-Elektrolyt, sondern immer nur spezielle Entwicklungen optimal für die jeweilige Anwendung.“
Noch kein dominantes Design bei E-Motoren
Dass es nicht nur bei Schmierstoffen und Batterie-Elektrolyten, sondern auch bei der Entwicklung der Elektromotoren selbst, derzeit nicht den einen Königsweg gibt, macht auch Malte Jaensch in seinem abschließenden Vortrag von electrive LIVE #34 deutlich. Der frühere Porsche-Entwickler ist Professor an der TU München, genauer gesagt am Lehrstuhl für Nachhaltige Mobile Antriebssysteme. Alleine schon diese Bezeichnung macht deutlich, dass die Transformation der Branche längst die universitäre Lehre erreicht hat: Von 1945 bis 2004 war es das „Institut für VKM und Kraftfahrzeuge“, dann bis 2021 der „Lehrstuhl für Verbrennungskraftmaschinen“. Und nun eben nachhaltige und mobile Antriebssysteme – das nur am Rande.
Bei der Entwicklung neuer Antriebe ging es bisher vor allem um Punkte, die Jaensch als „klassische Anforderungen“ bezeichnet – Drehmoment und Leistung, Gewicht, Volumen, Packaging, Kosten, um nur einige zu nennen. „Neue Anforderungen“ sind hingegen die Nachhaltigkeit bei den Rohstoffen und dem Produkt selbst sowie eine sichere Lieferkette.
„Lange Zeit war es in der Entwicklung ein zweidimensionales Spielfeld aus Performance und Kosten“, so Jaensch. „Die neue Dimension der Nachhaltigkeit und Lieferketten steht zum Teil im Widerspruch, muss aber im Lösungsraum des optimalen Antriebs gelöst werden.“
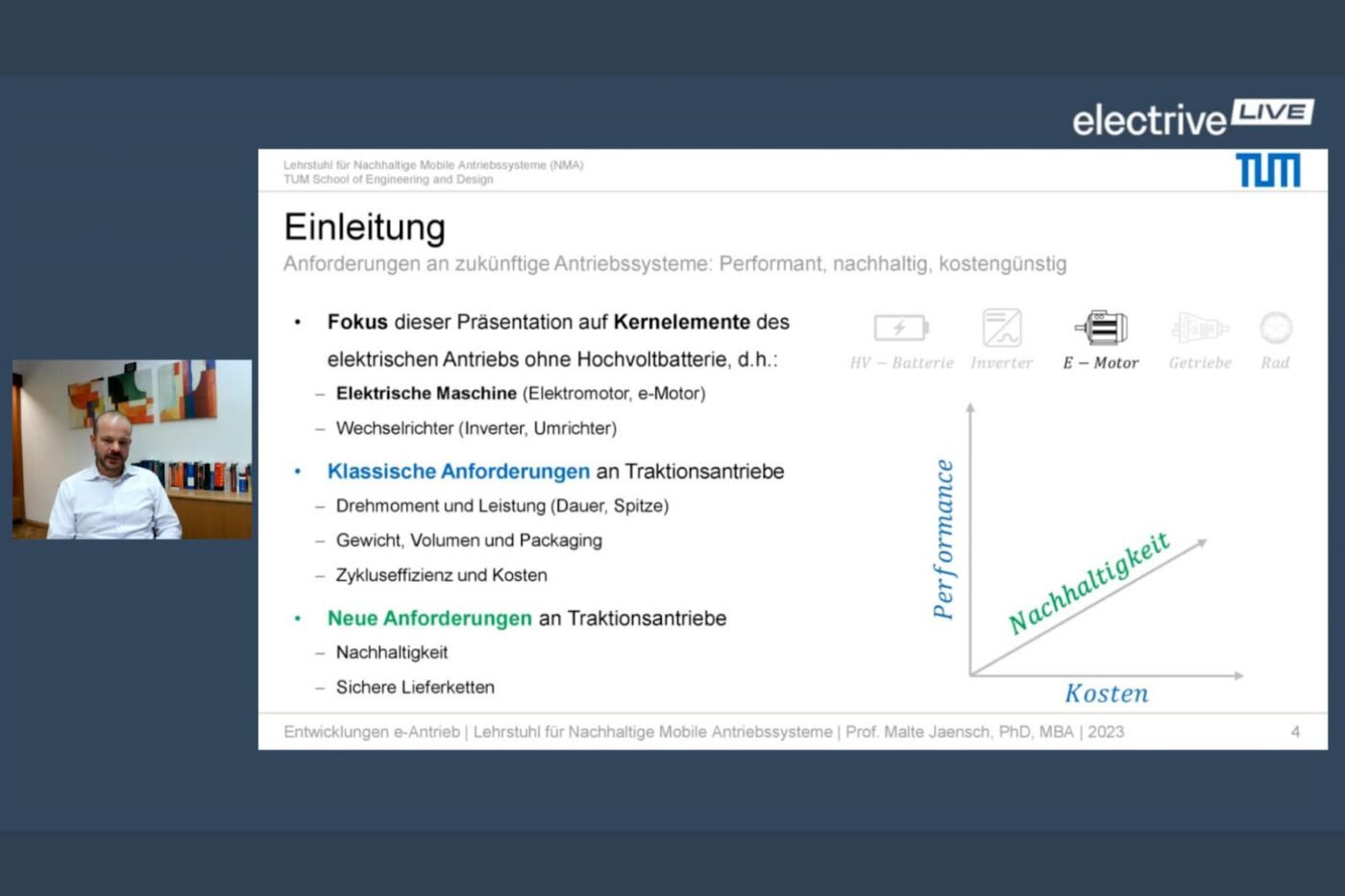
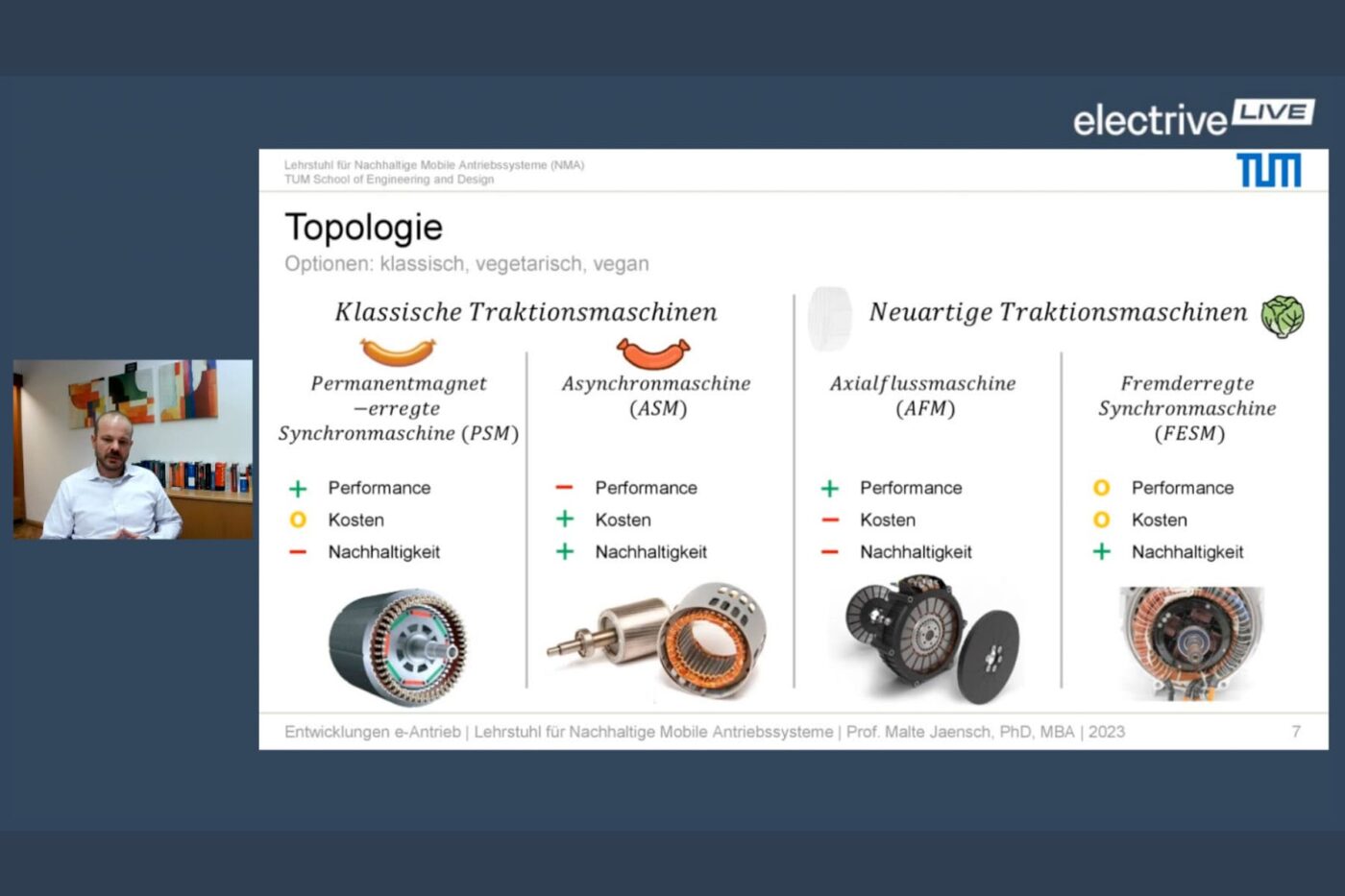
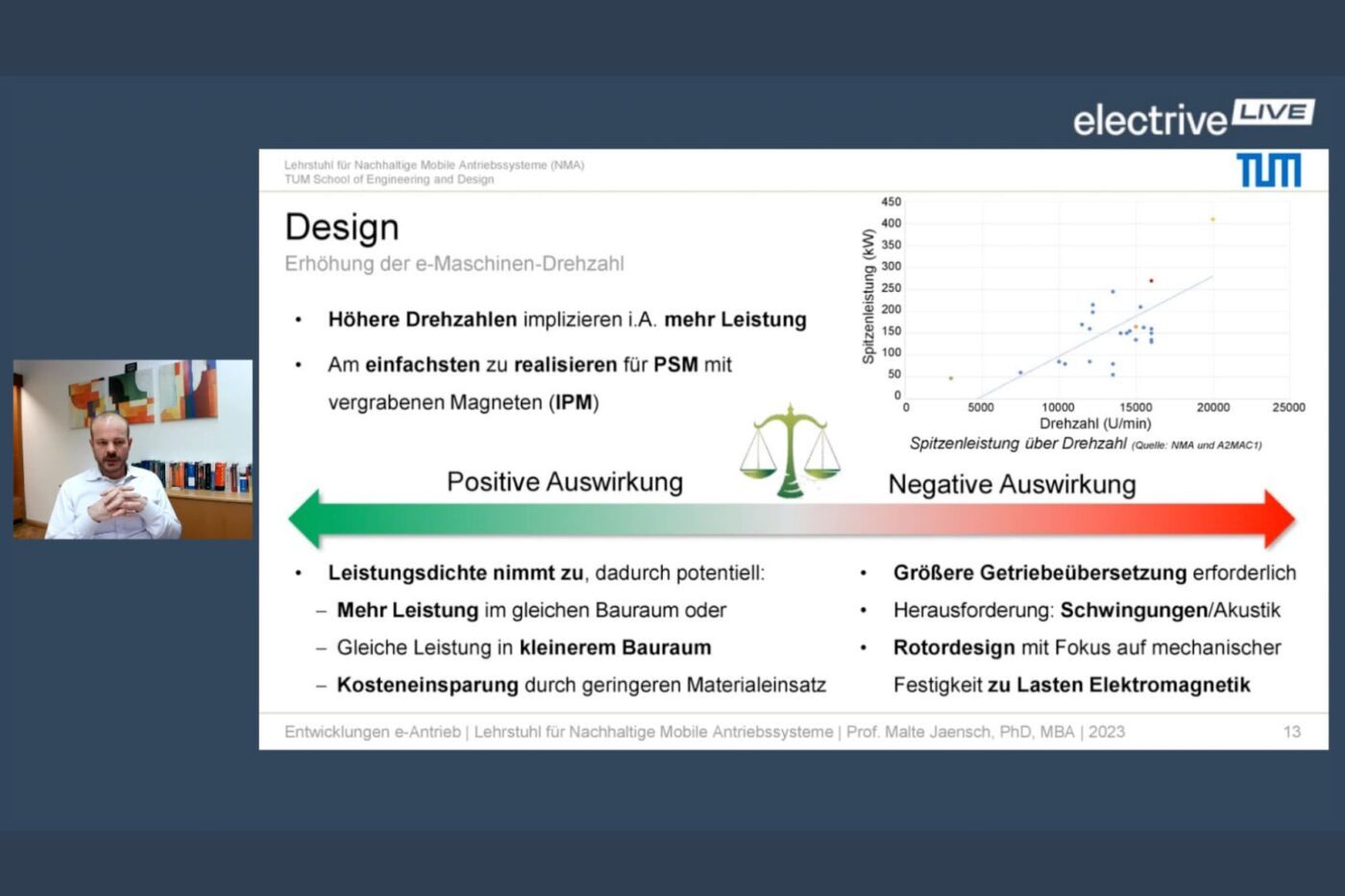
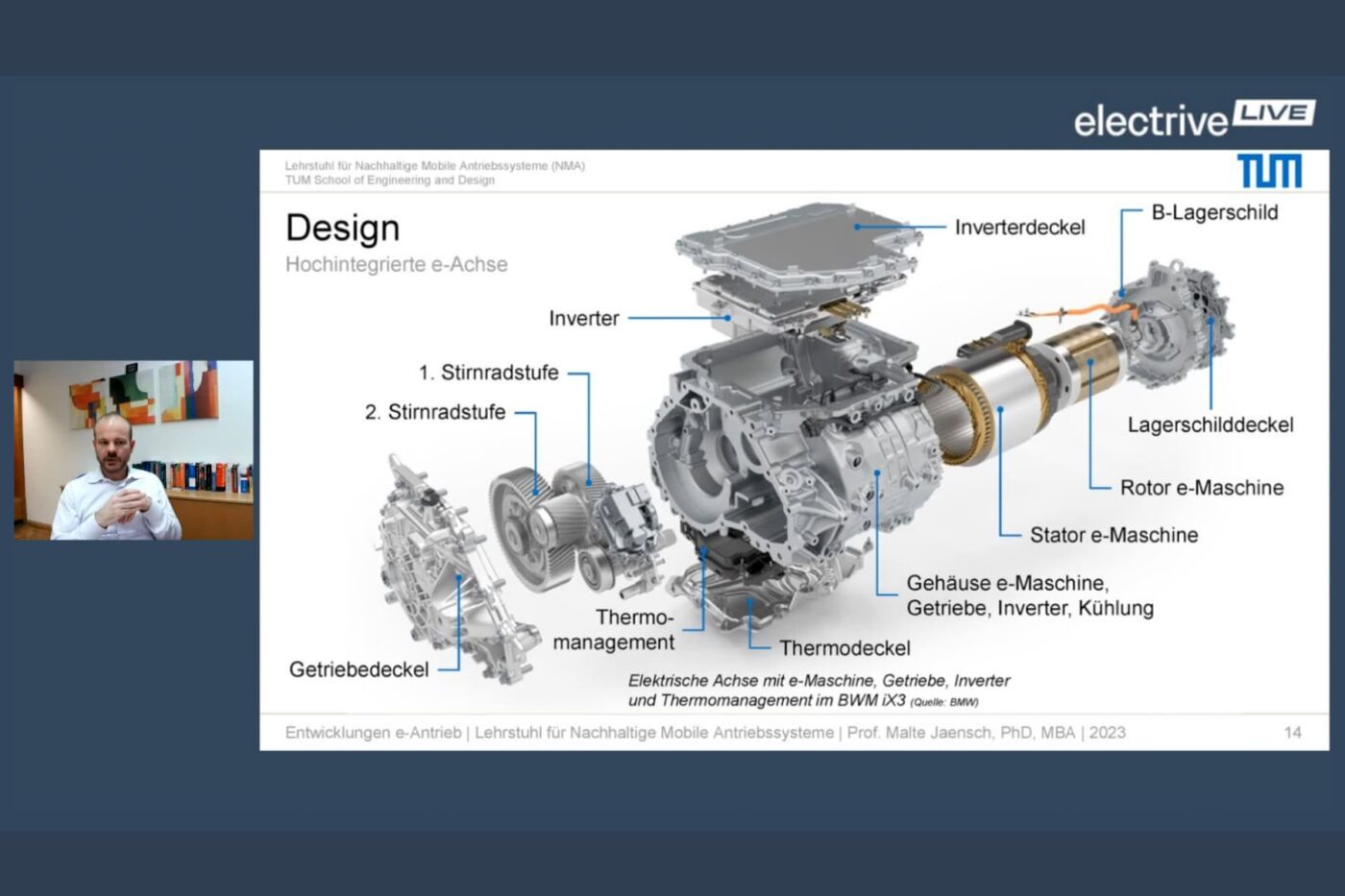
In seinem Vortrag konzentriert sich der Professor aus Zeitgründen auf den E-Motor selbst. Er und sein Team arbeiten aber auch an allen anderen Bereichen der E-Antriebe. Wie auch VW-Entwickler Krick hält Jaensch die Entwicklung bei den Invertern für enorm wichtig. „Bei der Entwicklung neuer elektrischer Antriebseinheiten können Entscheidungen im Wesentlichen entlang der drei Dimensionen Topologie, Design und Material/Subkomponenten getroffen werden“, erklärt der Professor. „Für ein optimal anforderungsgerechtes System müssen alle drei Dimensionen richtig gestaltet sein.“
Blicken wir auf die Hardware: Bei der Topologie der Motoren sieht Jaensch die heute in E-Autos verbreiteten Asynschonmotoren und permanenterregten Synchronmotoren für „klassische Kost“. Nicht neu als Funktionsprinzip für Elektromotoren, aber neu in der Elektromobilität sind Konzepte wie Axialflussmaschinen (AFM) und fremderregte Synchronmaschinen (FSM oder englisch EESM). Nur: Jede Topologie hat unterschiedliche Vor- und Nachteile bei Faktoren wie Performance, Kosten oder Nachhaltigkeit. „ Man muss sich überlegen, auf welchem Hügel man sterben will – die ideale Maschine gibt es nicht“, so Jaensch.
Zwei Beispiele: Die FSM ist zwar nachhaltiger, da sie ohne Dauermagnete auskommt und der Rotorstrom ermöglicht einen zusätzlichen Freiheitsgrad bei der Regelung. Der Rotor sorgt aber auch für zusätzliche Verluste, ein bis drei Prozent der Gesamtleistung gehen für die Erregung des Rotors drauf. Zudem muss die Energie erst in den Rotor übertragen werden, für den Überträger wird zusätzlicher, axialer Bauraum benötigt. In der Summe kommt die FSM nicht an die Effizienz der PSM heran. Ein Axialflussmotor ermöglicht zwar eine hohe Leistungs- und Drehmomentdichte und er zeichnet sich durch seine kurze, axiale Länge aus – bei einer vergleichbaren Effizienz zur PSM, da ebenfalls Permanentmagnete enthalten sind. Der vergleichweise große Durchmesser und die „mechanisch herausfordernde Konstruktion“ sprechen laut Jaensch aber gegen die AFM. Und: Der Rotor hat kein Reluktanzmoment, das gesamte Drehmoment stammt also aus der Magnetmasse, die entsprechend höher ausfällt.
Bei der zweiten Dimension, dem Design, berichtet der Professor vom Trend zu immer höheren Drehzahlen bei E-Maschinen. Das sei zwar gut für die Leistungsdichte und die Kosten (mehr Leistung bei weniger Materialeinsatz), habe aber auch Kehrseiten. So sind, wenn die Raddrehzahl gleich bleibt, größere Getriebeübersetzungen nötig und das andere Schwingungs- und Akustikverhalten muss berücksichtigt werden. Und der aus Jaenschs Sicht relevanteste Punkt: Um den höheren Drehzahlen Stand zu halten, muss der Rotor auf eine höhere mechanische Festigkeit ausgelegt werden, was zulasten der elektromagnetischen Eigenschaften geht. „Lohnt sich der Kompromiss zulasten mehr mechanischer Festigkeit? Das muss man sich in der Entwicklung immer fragen“, sagt Jaensch.
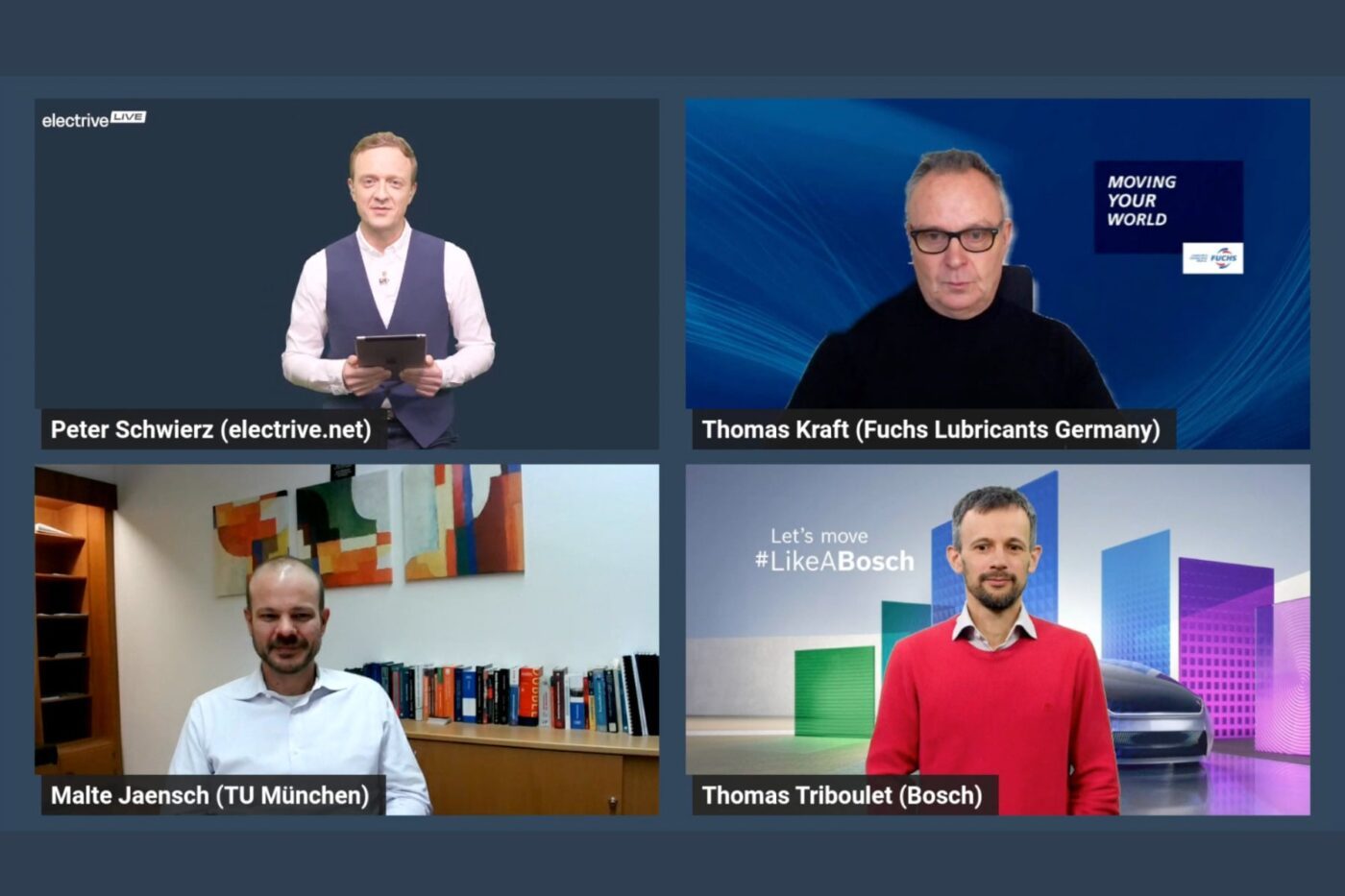
Weitere Punkte bei der künftigen Entwicklung betreffen die Kühlung. Traditionell erfolgt diese über eine Wassermantelkühlung rund um den Stator, wobei die im Motor entstehende Wärme erst einmal nach außen in den Kühlmantel abgeführt werden muss. Deutlich effizienter ist es, die Spulen direkt zu kühlen, dann aber auf Ölbasis – aber es ist auch konstruktiv aufwändiger. „Dort gibt es einige interessante Ansätze, in diesem Bereich wird sich in den kommenden Jahren viel tun“, erklärt der Professor. „Wenn man noch weitere Komponenten wie etwa den Inverter in den Kühlkreislauf nehmen will, wird es natürlich komplexer.“
Angesichts der steigenden Komplexität auf technischer und systemischer Ebene – Stichworte sind etwa Rohstoffbeschaffung, Lieferketten und geschlossene Kreisläufe – wird in all den Vorträgen klar: Die Transformation ist eine enorme Herausforderung, die Stimmung in der Branche ist durchwachsen, die Risiken, von anderen Playern überholt zu werden, sind unverkennbar. Denn wie Jaensch berichtet, entsteht in China nicht nur eine wettbewerbsfähige E-Auto- und Batterieindustrie, sondern auch ein Zuliefer-Netzwerk, das selbst schnell und günstig Komponenten entwickelt.
Drei Wünsche für 2024
In der Diskussionsrunde blickt Jaensch aber auch nach vorne: „Jede Veränderung ist auch eine Chance: Nachhaltigkeit ist eine weitere Dimension, die ich bei der Entwicklung beachten muss – das macht mein Leben zunächst komplizierter. Wenn ich mir aber einen Vorteil erarbeiten kann, ist es definitiv eine Chance. Auch für die europäische Industrie.“ Fuchs-Manager Thomas Kraft pflichtet dem bei: „Wir sehen die Nachhaltigkeit als weitere Form, uns zu differenzieren.“
Nur: Zumindest zu Anfang sind die nachhaltigen Lösungen meist teurer, weil sie nur in geringen Stückzahlen verfügbar sind und nicht in den optimierten, erprobten Prozessen hergestellt werden können. Doch wer zahlt dafür? „Die Endverbraucher werden sich an höheren Kosten für nachhaltige Produkte kaum beteiligen – das sehen wir in anderen Branchen“, sagt Bosch-Manager Triboulet. „Schon heute zahlen Energiekonzerne oder Stahl- und Aluminiumhersteller 70 bis 100 Euro pro Tonne CO2. Dort geht es um Beträge, die wirtschaftlich relevant sind und zu einem Geschäftsmodell werden, wenn wir Millionen-Beträge einsparen können.“
Und welchen Wunsch unsere drei Experten zu Weihnachten haben? „Ich wünsche mir, dass viele meiner Kolleginnen und Kollegen kreative Ideen haben, auf die ich selber nicht gekommen bin“, sagt Jeansch. Triboulet wünscht sich „klare und mutige gesetzliche Rahmenbedingungen, damit wir keine Zeit verlieren“. Und Thomas Krfat ergänzt:„Ich würde mir viel mehr kostengünstige E-Autos auf dem Markt wünschen – und Optimismus für die Branche.
In diesem Sinne wünschen wir von electrive frohe Weihnachten, bedanken uns bei allen Referentinnen und Referenten, die in diesem Jahr bei electrive LIVE aufgetreten sind – und natürlich bei allen Sponsoren und Gästen. Im Januar geht’s mit unseren Online-Konferenzen weiter. Alle Infos dazu finden Sie immer hier.
1 Kommentar