Kamenz: Exklusiver Besuch in der Daimler-Batteriemontage
Die Batteriemontage von Daimler in Kamenz ist der Grundstein für einen weltweiten Akku-Produktionsverbund – mit sieben Fertigungsstätten auf der ganzen Welt. Der Branchendienst electrive.net konnte nun die Montage von Batterien von Mercedes Benz begleiten. Ein exklusiver Werksbesuch.
* * *
Noch herrscht rund um die neuen Hallen in Kamenz ordentlich Betrieb. Bauarbeiter und Handwerker erledigen letzte Arbeiten im Außenbereich des Gebäudes. Intensiv wird insbesondere noch am Rohbau der neuen Kantine hantiert. Ruhiger geht es in den neuen Fabrikhallen zu. Da die Hallenfläche zum Zeitpunkt unserer Werksbesichtigung noch nicht komplett mit Produktionsanlagen gefüllt ist, wird beim Betreten die Dimension der inklusive Logistikflächen rund 30.000 qm großen Halle besonders deutlich. Dabei schweift der Blick flächenmäßig nur über die Hälfte des neuen Werks 2. Hinter einer Brandschutzwand befindet sich eine zweite Halle mit identischen Ausmaßen. Durch die Erweiterung vervierfacht sich die Produktions- und Logistikfläche am Batteriestandort Kamenz auf insgesamt rund 80.000 qm. Im benachbarten Werk 1 produziert die Mercedes-Benz-Tochter Deutsche Accumotive schon seit 2012 Antriebsbatterien für Hybrid- und Elektrofahrzeuge in Serie.
Während im neuen Werk Auszubildende an Lerninseln geschult werden, sind einige Mitarbeiter an der sogenannten Launch-Line beschäftigt. Dort sollen schon bald die ersten Serienbatterien für den Mercedes Benz EQC montiert werden. Nach Auskunft von Erhard Schletterer, dem Geschäftsführer der Deutschen Accumotive, läuft die Launch-Line noch im ersten Quartal an. Weitere, stärker automatisierte Produktionslinien sind ebenfalls im zweiten Hallenschiff erkennbar und werden parallel in diesem Jahr hochgefahren.
Zweigeteilte Batteriemontage
Sämtliche Arbeitsschritte der Batteriemontage sind im Werk 1 zu sehen. Dort produziert die Daimler-Tochter unter anderem Aggregate für den Smart ED, den eVito oder 48-Volt-Systeme. Im Prinzip ist die Montage einer Batterie zweigeteilt: in die Herstellung des sogenannten Frontends (Moduls) sowie des Backends. Bei der Frontend-Montage werden aus einzelnen Zellen sogenannte Zellblöcke gemacht. Deren Dimension ist von der Anwendung abhängig. Beim 48-V-System stecken jeweils zwölf Zellen in einem Block, bei einer Hybridbatterie sind es 50. Ein wichtiger Arbeitsschritt ist hier die Herstellung von Schweißverbindungen. So müssen unter anderem die Pole verschweißt werden oder auch die sogenannten Zellverbindereinheiten. Abschließend wird der Zellblock mit weiteren Anbauteilen komplett montiert.
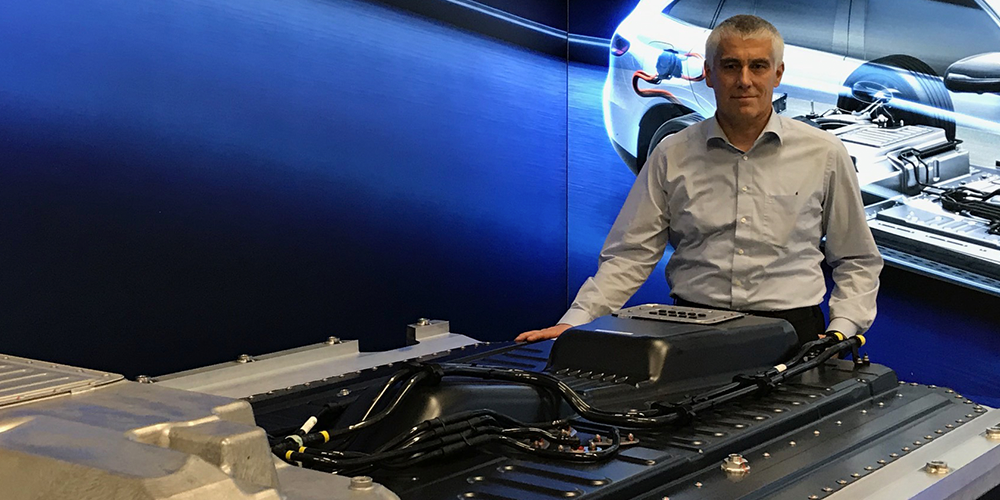
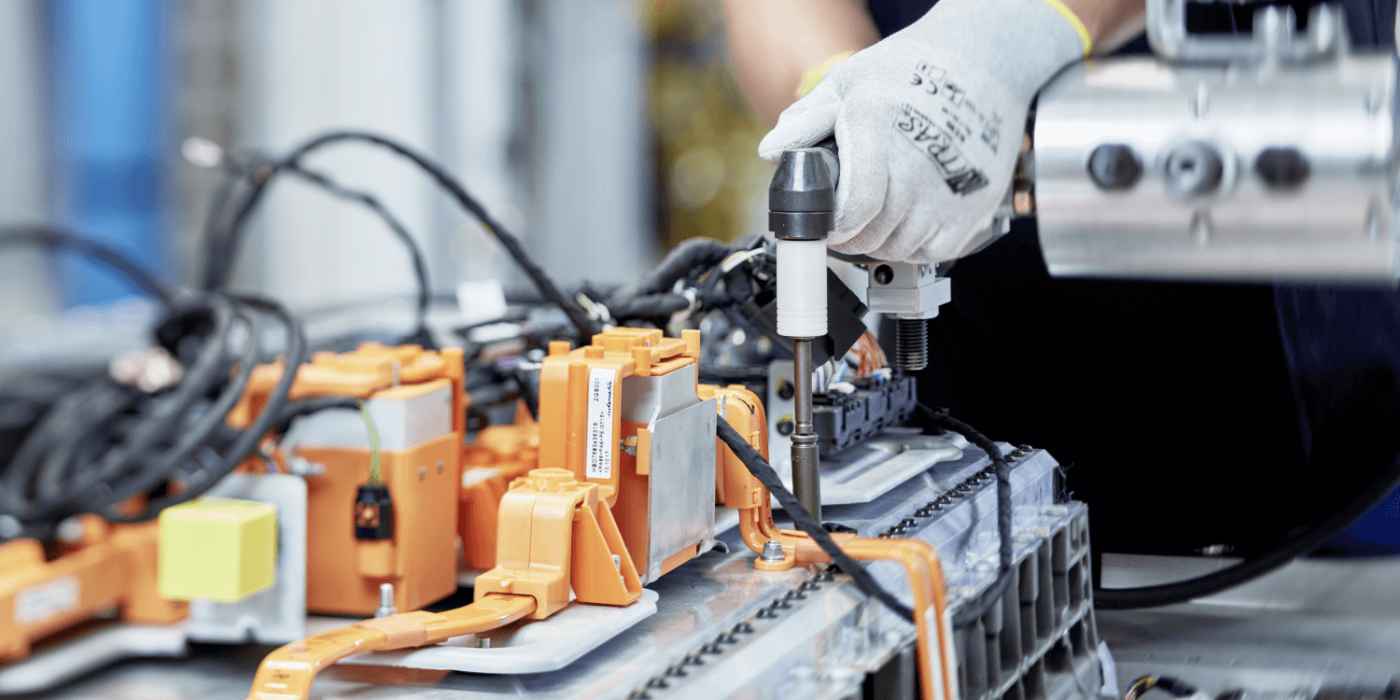
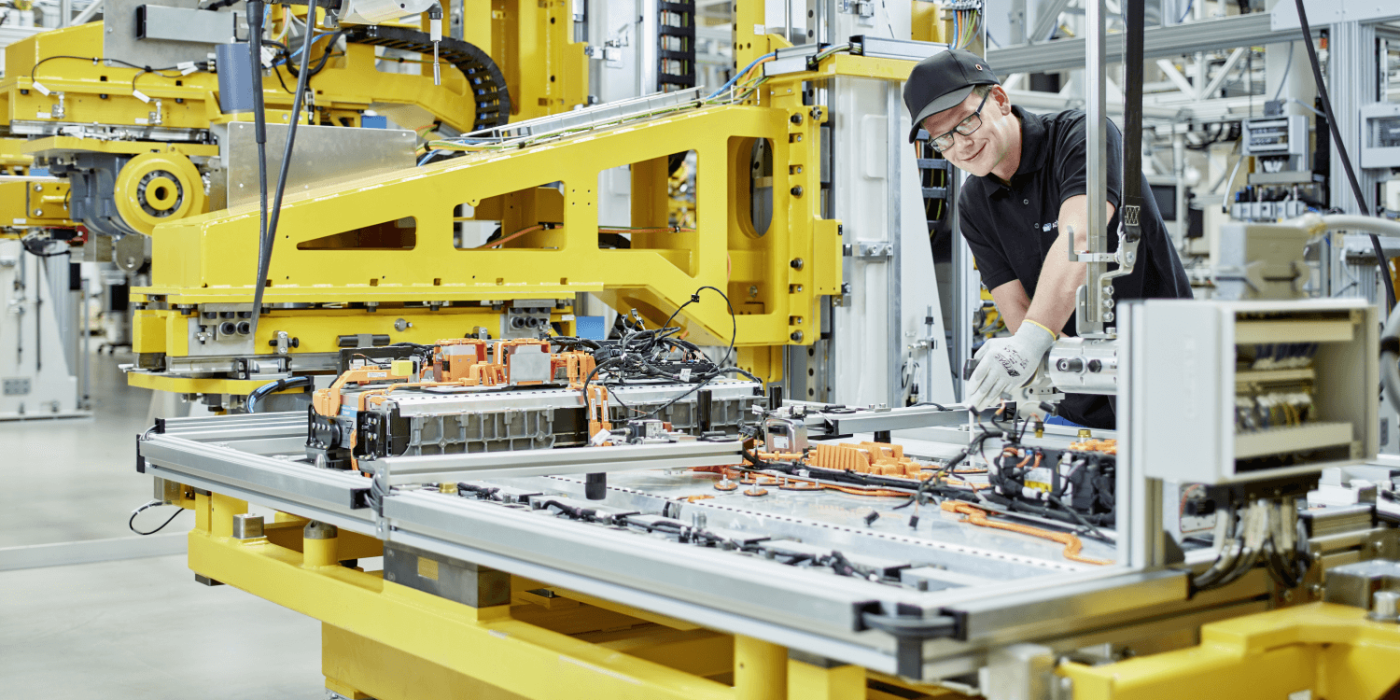
Bei der Backend-Montage entsteht aus den Blöcken das Endprodukt Batterie. In einem Arbeitsschritt etwa wird Wärmeleitpaste auf das Gehäuseunterteil aufgetragen, in einem anderen die Blöcke in das Unterteil eingesetzt. Anschließend müssen noch die Hochvolt-Verkabelung angebracht und diverse weitere Komponenten wie die Kühlung eingesetzt werden, bevor die Batterie mit dem Oberteil verschlossen werden kann. Zum Schluss durchlaufen die fertigen Speicher einen Dichtigkeitstest mittels Helium sowie einen sogenannten End-of-line-Test zur Prüfung der elektrischen Funktionalität.
„In unserer Batteriefertigung haben wir einen Mix aus automatisierten und klassischen Montagetätigkeiten“, erläutert Schletterer, der zusätzlich zu seiner Geschäftsführer-Position als Leiter Produktion eDrive in der Daimler AG für den Auf- und Ausbau des internationalen Produktionsnetzwerks Batterien sowie für die Herstellung von Brennstoffzellensystemen zuständig ist. Er weist darauf hin, dass trotz der erheblichen Größen- und Gewichtssteigerung der im Werk 2 produzierten EQC-Batterien die Linien im Frontend-Bereich einen ähnlich hohen Automatisierungsgrad aufweisen wie in der Produktion der Smart-Batterie.
Neue Dimension bei der EQC-Batterie
Um zu erfassen, welche Entwicklungsschritte die Batterietechnologie bereits in kurzer Zeit hinter sich gebracht hat, lohnt sich ein Blick auf die Produktdaten. Die seit 2016 in Serie produzierte Smart-Batterie kommt auf einen Energieinhalt von 17,6 kWh und eine Spitzenleistung von 76 kW (Dauerleistung: 47 kW). Im etwa 170 Kilo schweren Aggregat stecken genau 96 Zellen.
Die im eVito verbaute Batterie kommt auf 41,4 kWh und besteht aus drei Plug-in-Hybrid-Modulen mit je 100 Zellen und einem Energieinhalt von je 13,8 kWh. Eines dieser Module kommt als Batterie u.a. in der S-Klasse zum Einsatz. Die seit Juni 2017 in Serie produzierte Batterie kommt auf ein Gewicht von 110 kg. In einer anderen Dimension bewegen sich die Werte der neuen EQC-Batterie: In dem 657 kg schweren Hochvoltspeicher sind 384 Zellen untergebracht. Die Batteriekapazität beträgt 80,5 kWh und die Spitzenleistung liegt bei 320 kW (Dauerleistung: 150 kW).
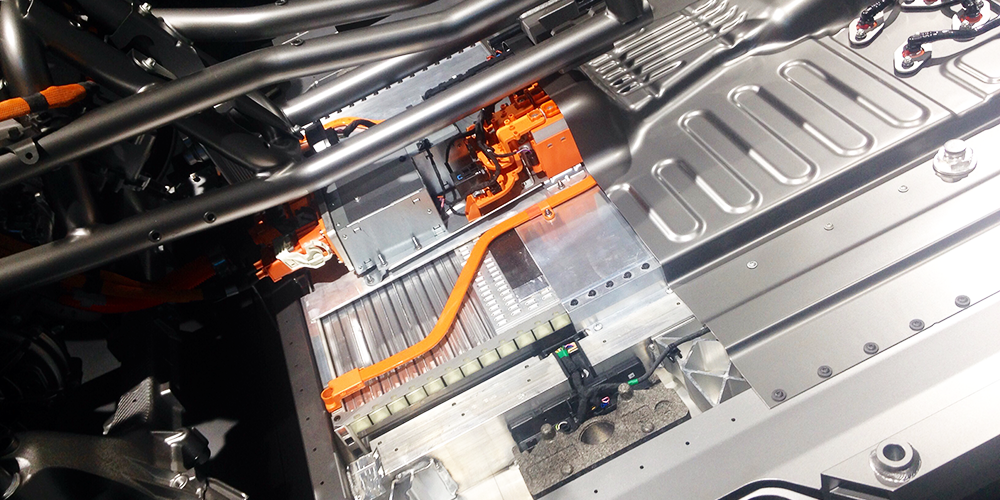
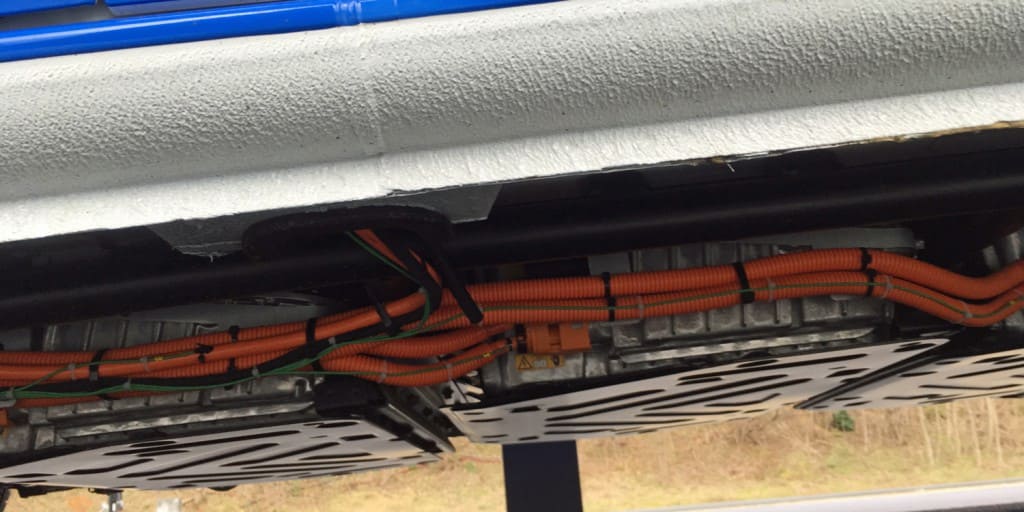
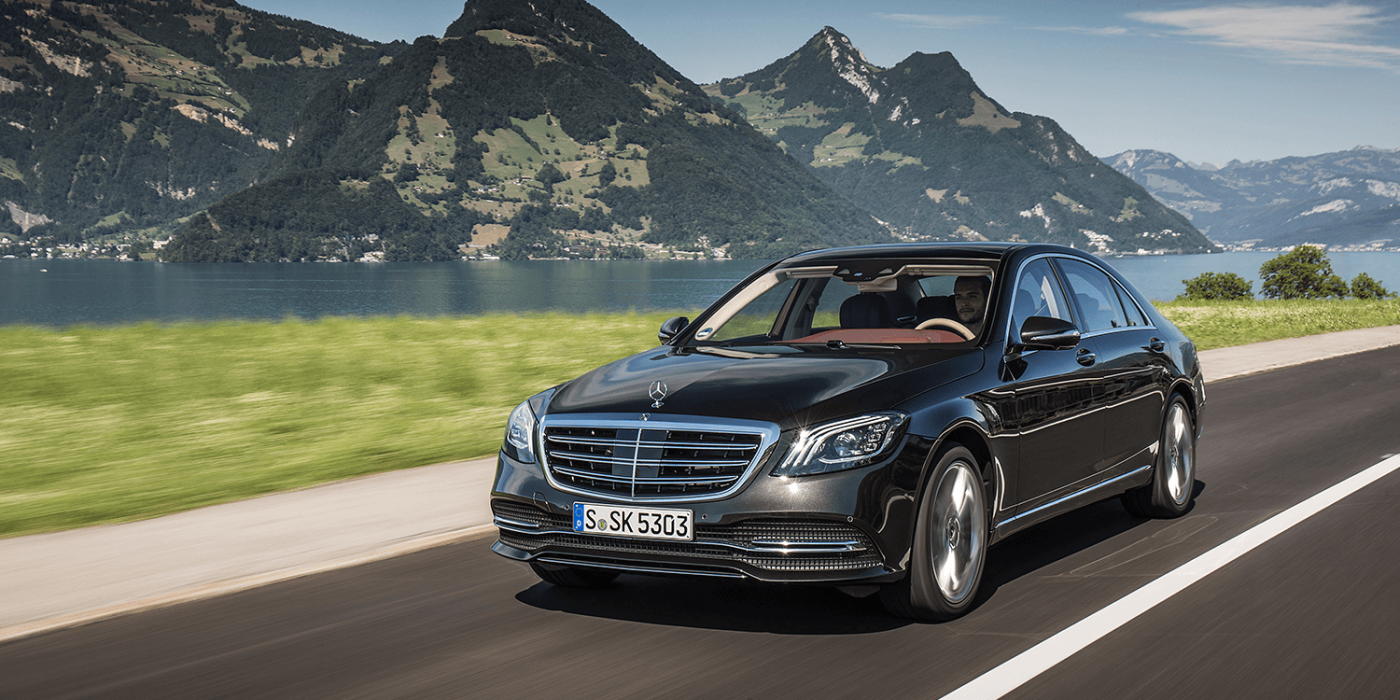
In der neuen Fertigung des Spitzenaggregats des Stuttgarter Konzerns kommen verschiedene neue Technologien zum Einsatz, wie eine optimierte Produktionslogik mit Boden- und Fließfertigung sowie Fahrerlosen Transportsystemen (FTS). Am Produktionsfluss und der Linienanordnung orientiert sich auch das gesamte Gebäudedesign. Zudem werden spezielle Montageeinrichtungen die Werkstücke den Werkern ergonomisch günstig bereitstellen. Wenig verwunderlich ist die Verwendung moderner Industrie-4.0-Technologien, wie die digitale Steuerung und Nachhaltung der Produktionssysteme. Diese garantiert unter anderem die vollständige Rückverfolgbarkeit der in jeder ausgelieferten Batterie verbauten Komponenten inklusive der kompletten Fertigungsdaten. Laut Schletterer ist man in diesem Bereich weltweit führend. Doch nicht nur hier verweist er auf Alleinstellungsmerkmale. Man arbeite zudem an sehr flexiblen Linien, die in der Lage sind, mehrere Baureihen herzustellen. Nähere diesbezügliche Fertigungsgeheimnisse sind dem Geschäftsführer jedoch nicht zu entlocken.
Qualifizierung für das Arbeiten unter Hochvolt
Eine große Herausforderung in Kamenz ist das schnelle Personalwachstum: Bis Ende 2018 verdoppelte sich die Zahl der Beschäftigten auf rund 1.000 – ein Ziel, das man ein Jahr früher erreichte als ursprünglich geplant. „Die Mitarbeiter verfügen mehrheitlich über einen elektrotechnischen Hintergrund“, betont Schletterer. Dennoch überlässt man bei Daimler hierbei nichts dem Zufall. „Unsere Produktionsanlagen sind nach höchsten Sicherheitsstandards gestaltet. Außerdem durchlaufen unsere Mitarbeiter spezielle Qualifizierungsprogramme, in denen sie intensiv im Umgang mit Hochvolttechnologie unter Produktionsbedingungen geschult werden“, berichtet der Geschäftsführer.
Die Bedeutung des Standorts ist auch an der Investitionssumme ablesbar. Von dem insgesamt für den globalen Batterie-Produktionsverbund vorgesehenen Investitionsvolumen von über einer Milliarde Euro fließt rund die Hälfte nach Kamenz. Der Verbund besteht aus neun Fabriken an sieben Standorten auf drei Kontinenten. Nach dem Start der Serienproduktion der zweiten Fabrik in Kamenz in diesem Jahr folgt die Batteriefertigung in Peking. Auch dort werden derzeit bereits die ersten Produktionsanlagen aufgestellt. Zudem sieht die Planung zwei weitere Fabriken in Stuttgart-Untertürkheim, eine am Standort Sindelfingen, sowie jeweils eine in Bangkok und Tuscaloosa (USA) vor. Darüber hinaus wird Daimler auch im polnischen Jawor eine Batteriefabrik bauen. Dabei produzieren die Werke jeweils für den lokalen Markt. Ein weltweit geltender Standard für Batteriefabriken hinsichtlich „Setting und Organisation“ soll dem schwäbischen Automobilkonzern eine einheitliche Produktqualität garantieren.
Konsequente Weiterentwicklung der Zelltechnologie
Besonderes Augenmerk liegt freilich auf der wichtigsten Komponente einer Batterie: der Zelle. Diese werden mit den Zulieferern vorentwickelt und gemäß einem Komponentenlastenheft spezifiziert, dazu zählen Parameter wie Leistungskenndaten. „Wir wissen schließlich was das Gesamtsystem können soll“, erläutert Geschäftsführer Schletterer. Die Kompetenzen zur technologischen Evaluierung von Zellen sowie Forschungs- und Entwicklungsaktivitäten sollen konsequent ausgeweitet werden, teilt der Stuttgarter Automobilkonzern dazu mit. Dies betreffe sowohl die Optimierung der aktuellen Generation der Li-Ionen Systeme, als auch die Weiterentwicklung der am Weltmarkt zugekauften Zellen sowie die Erforschung der nächsten Generation von sogenannten Post-Lithium-Ionen-Systemen.
Für Aufsehen sorgte kurz vor Jahresschluss der Vertragsabschluss über den Zukauf von Batteriezellen im Wert von 20 Milliarden Euro. Mit der bis ins Jahr 2030 geltenden Beauftragung stelle man die Belieferung von Zellen mit der jeweils neusten Technologie sicher, war in der entsprechende Pressemitteilung zu lesen. Man wolle beim Bezug so flexibel sein, dass immer der Zulieferer mit dem besten Preis-Leitungs-Verhältnis ausgewählt werden könne, begründet Geschäftsführer Schletterer die strategische Ausrichtung. Unabhängig davon wird auf sein Team in Kamenz in den nächsten Jahren viel Arbeit zukommen.
2 Kommentare